Especial Baterías Parte III: Arquitectura de packs
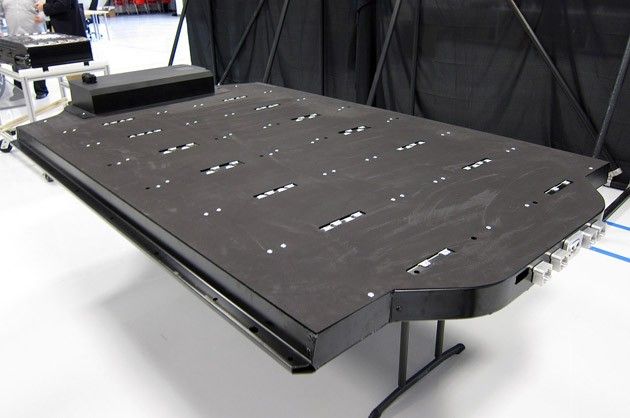
Relacionadas
Especial Baterías Parte I: El ABC de las baterías
Especial Baterías Parte II: Los packs de baterías
Ya hemos comentado en anteriores artículos que los packs de baterías están compuestos por conjuntos de celdas individuales interconectados de muy diferentes maneras. En este artículo vamos a ver cómo son esos conjuntos e interconexiones que los conforman y algunas consideraciones que me parecen que pueden ser interesantes.
Todos los parámetros de un pack están muy relacionados entre sí por lo que unos factores afectan a otros y hay que alcanzar algunos compromisos en el proceso de diseño, de los cuales el más importante por desgracia hoy día es el precio. Vaya por delante que no soy un completo experto y que estas son mis apreciaciones desde mi entendimiento de esta tecnología.
En muchas ocasiones comentamos que si tal o cual coche debería llevar packs de cierto número de kWh, que porque no hay una versión del Leaf de 40 kWh, o un Zoe de 30 kWh, etc. Olvidamos a menudo que las celdas tienen cantidades discretas de voltaje, potencia y capacidad, por no hablar de su tamaño, peso, durabilidad en ciclos y precio, por lo que las combinaciones posibles no son infinitas sino limitadas.
El primer factor limitante de todas esas combinaciones es la tensión nominal que requerimos a nuestro pack, que dependerá de la tensión de trabajo del motor y de la electrónica de potencia. Así que lo primero a considerar en el diseño es la tensión del elemento usado como mínima expresión de almacenamiento en nuestro pack.
Tomemos como ejemplo que necesitamos por las características de nuestro motor y controlador una tensión nominal de 360 voltios, y que los elementos que hemos elegido por precio, durabilidad y potencia para nuestra batería tienen una tensión nominal de 3,6V. Para conseguir ese voltaje de pack de 360 V necesitaremos al menos 100 de esas celdas conectadas en serie (360 V / 3,6V = 100), también denominado 100S.
Ya tenemos el voltaje necesario, pero ahora nos falta alcanzar la potencia y capacidad necesarias para mover el vehículo a la velocidad adecuada y durante el tiempo o kilómetros deseados. Si por requerimientos de diseño hemos decidido que la capacidad de nuestro pack debe ser de 24 kWh necesitaremos entonces que cada uno de los 100 elementos en serie pueda entregar 66,66 Ah (24 kWh / 360 V = 66,66 Ah). Y aquí es donde la cosa se lía, ya que podemos elegir dos caminos muy diferentes en la arquitectura del pack para alcanzar ese objetivo.
Packs con “pocas” celdas grandes
Utilizar celdas o elementos grandes es la manera más sencilla de fabricar un pack y es la empleada por la inmensa mayoría de fabricantes de vehículos híbridos y eléctricos, como por ejemplo Nissan, Renault, los trillizos y muchos otros. Si para ese pack de 24 kWh y 360 V conseguimos 100 elementos de 66,66 Ah y los montamos en serie entonces ya lo tenemos listo.
El Nissan Leaf, por poner un ejemplo muy conocido, usa algo parecido a ese diseño. Lleva 48 módulos conectados en serie, y cada uno de esos módulos lleva cuatro celdas y es de 7,6 V (2 celdas en serie de 3,8V) y 66,2 Ah (dos grupos en paralelo de 33,1 Ah). Su nomenclatura es 48S 2P 2S. En resumen, obviando los módulos el Leaf lleva dos grupos paralelos de 33,1 Ah y cada uno de esos grupos lleva 96 celdas de 3,8 V en serie. En total 3,8 V x 96 celdas son los 364,8 V del pack y 364,8 V x 33,1 Ah x 2 son los 24 kWh de capacidad del pack (24.150 Wh). Sólo 192 celdas en total.
Packs con “muchas” celdas pequeñas
La otra aproximación al problema es precisamente la opuesta, utilizando muchos elementos pequeños y de poca capacidad, por ejemplo de unos 3 Ah cada uno. Continuando con el ejemplo anterior de nuestro pack de 24 kWh y celdas de 3,6 V, para llegar a 66,66 Ah necesitaremos grupos de 23 unidades de 3 Ah (66,66 Ah / 3 Ah = 22,22, redondeando 23) conectadas en paralelo y después montaremos 100 de estos grupos en serie para tener el pack completo, tipo 100S 23P, 2300 celdas contra las 192 que monta el Leaf para la misma capacidad.
Este es el tipo de arquitectura utilizada en muchos packs de ciclomotores y bicicletas. Tesla es en automoción el perfecto ejemplo de esta otra arquitectura de pack, ya que usan miles de celdas pequeñas típicas de las baterías de ordenador portátil, modelo 18650 (cilíndricas de 18 mm de diámetro y 65 mm de longitud) de 3,6 V nominales y unos 3100 mAh en el caso del Model S. Tesla utilizó este tipo de arquitectura por la gran disponibilidad de este tipo de celdas, ya que se fabrican por millones y podían conseguir precios más competitivos. También por su mayor energía específica y una mayor facilidad de refrigeración gracias a su factor de forma cilíndrico.
Ventajas y desventajas de cada arquitectura
La principal ventaja de un pack basado en celdas o elementos grandes es que a nivel constructivo el número de conexiones y la complejidad de todos los sistemas, como BMS y refrigeración es mucho menor. En el Leaf sólo hay 192 celdas a controlar mediante BMS luego solo hay un puñado de interconexiones. Y la refrigeración activa ni siquiera existe. Simplicidad máxima.
Pero esa simplicidad tiene sus pegas. Si mañana alguien en Nissan decide que se va aumentar la capacidad del Leaf ya tienen un problema. Si quieren seguir usando los mismos módulos y celdas, al estar obligada a mantener la tensión de 364,8 V tendrían que poner otros 48 módulos en serie, en paralelo con los anteriores. En total 96 módulos, y eso son necesariamente 48 kWh de capacidad en total. Eso es ahora mismo imposible porque, además de ser 182 kg más de peso, y disparar el precio de paso, no cabe ni un solo módulo más en el espacio del pack, mucho menos otros 48. Flexibilidad nula.
Hay un problema añadido en el hecho de usar celdas grandes, y es que en caso de fallo grave de una de nuestras celdas o módulos el pack entero se resiente gravemente en potencia y capacidad o puede directamente dejar de funcionar. En la practica el Leaf lleva dos grupos de 96 celdas en paralelo. Imaginad que una sola de las celdas por la razón que sea falla totalmente. La capacidad del pack bajaría directamente a la mitad.
Estos problemas en cambio se mitigan con la aproximación de celdas pequeñas. En primer lugar el pequeño tamaño de sus celdas permite una gran flexibilidad en la forma del pack. Tesla ha sabido aprovechar esa característica convirtiendo su pack de baterías en un paquete totalmente plano en el suelo del vehículo de tan sólo unos 10 centímetros de grosor, dejando una gran espacio libre en el resto del coche.
Por otro lado esa flexibilidad se extiende a la capacidad de los packs. A 3,6 V por celda tener 360 voltios nominales sólo requiere de 100 celdas como ya hemos visto, pero con celdas de 3 Ah esas 100 celdas suponen una capacidad redondeando un poco para abajo de 1 kWh. Así que en teoría podríamos hacer packs en cualquiera de los múltiplos de 1 kWh, añadiendo en cada paso solo unos 6 o 7 kg de peso al pack. Podríamos hacer packs de 24 kWh, o de 25, o de 34, prácticamente lo que nos dé la gana.
En cuanto a la fiabilidad también aumenta. Si tenemos para el ejemplo de los 24 kWh de antes 23 grupos en paralelo de 100 celdas en serie y una celda falla totalmente nuestro pack pierde sólo un 4,35% (100/23) de su capacidad, no la mitad.
Por otra parte si bien es cierto que las celdas pequeñas disipan mejor el calor también complican los sistemas de refrigeración. No es lo mismo enfriar las 200 o 300 celdas de la mayoría de coches actuales que las cerca de 8000 del Model S de 85 kWh. Además cuanto mayor es el número de elementos el BMS (Battery Management System) se complica más todavía. Y desde luego todo esto es bastante más caro que en un pack hecho de la otra manera más simple.
Capacidad, potencia y durabilidad
Unas últimas observaciones quiero hacer respecto a la capacidad de los packs que son independientes de la arquitectura utilizada, aunque ya las hemos comentado en alguna ocasión antes.
Cuanto más capaz es un pack tanto más potente es. Imaginad que nuestras celdas nos permiten puntas de corriente de 5C. En un pack de 24 kWh cuando las celdas trabajen a 5C el pack nos entregará 120 kW de potencia. Con el mismo tipo de celdas un pack de 40 kWh a 5C nos dará 200 kW de potencia.
Además un pack más capaz nos proporcionará una mayor durabilidad. Imaginad un coche con 24 kWh que nos permite hacer de media 150 km en un ciclo completo de carga y descarga, y que nuestras celdas soportan 1000 ciclos antes de ver su capacidad mermada al 75%. Si hacéis 25.000 km al año en 6 años habréis hecho 150.000 km y vuestra batería habrá pasado por unos 1000 ciclos completos por lo que habrá perdido aproximadamente un 25% de capacidad. Además si nuestro motor es de 80 kW de potencia pico las celdas del pack trabajarán en ocasiones a corrientes de algo más de 3C.
Ahora imaginad que ese mismo coche tiene 40 kWh. Por regla de 3 un ciclo os permitirá hacer unos 250 km. En 6 años haréis los mismos 150.000 km de antes pero vuestra batería, hecha con el mismo tipo de celdas, sólo habrá pasado por unos 600 ciclos completos. El DOD diario será mucho menor y habrá perdido mucha menos capacidad que la de 24 kWh. Y con el mismo motor de 80 kW nuestras celdas trabajarán como máximo a corrientes de 2C, luego sufren menos.
Conclusiones
Como veis cuanto mayores y capaces sean las unidades básicas de batería usadas menos flexible es la capacidad de nuestro pack y es más sensible a fallos, pero también es más sencilla y barata su construcción. Por otra parte el uso de muchas celdas pequeñas complica el aspecto de la interconexión de estas, aumenta la complejidad del BMS y de la refrigeración de las mismas pero nos permite un control más fino de la capacidad y potencia, y mejores cifras de energía específica y densidad del pack.
También podéis ver que al parecer la mayoría de marcas confían en una futura actualización de las celdas que usan para conseguir mayor autonomía ya que en general no destinan espacio de sobra a las baterías. Es por eso que no vemos apenas variantes en las baterías ofertadas con nuestros modelos eléctricos, con Tesla como casi única excepción.
Así que ya sabéis, la próxima vez que penséis en por qué Nissan no mete más batería al Leaf, o Renault al Zoe, o Ford al Focus EV o cualquier otro caso, pensad en ello dos veces. Tal vez no es que no quieran, tal vez no es por el coste (aunque también), a lo mejor es simplemente que no pueden. Al menos no sin cambiar de celdas, de arquitectura, de BMS, de refrigeración, etc.
En un próximo artículo de esta serie echaremos un vistazo a los BMS, a ver de que tipos existen y que es exactamente lo que hacen. Espero no haberos aburrido y nos vemos en la próxima entrega de este repaso.
Este artículo está escrito a medias con Gonzalo Chomón, de www.rcmaterial.com, a quien le agradezco sinceramente el tiempo y esfuerzo dedicados y sus observaciones.
—–
Artículos relacionados:
Especial Baterías Parte I: El ABC de las baterías
Especial Baterías Parte II: Los packs de baterías
© Foro Coches Eléctricos | Este feed es de uso personal, sí quieres hacer un uso comercial contacta con nosotros.