El proceso de fabricación de BMW i8
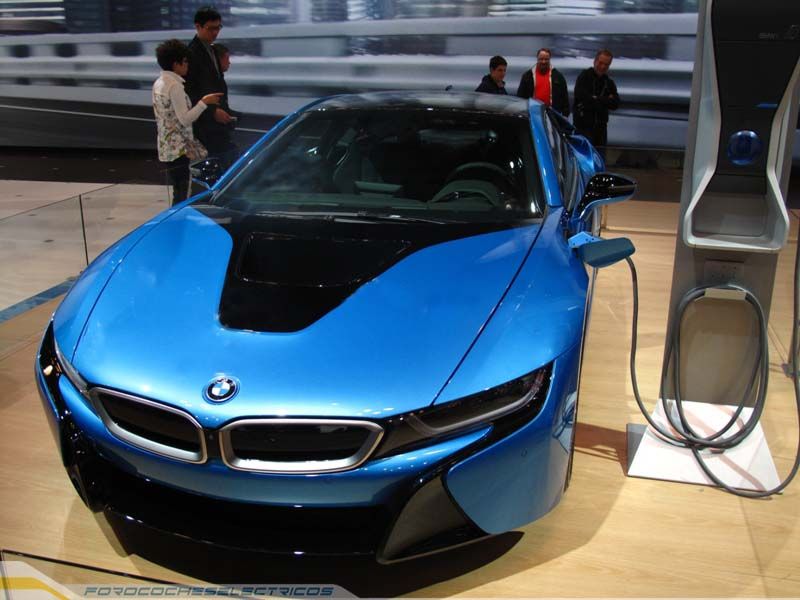
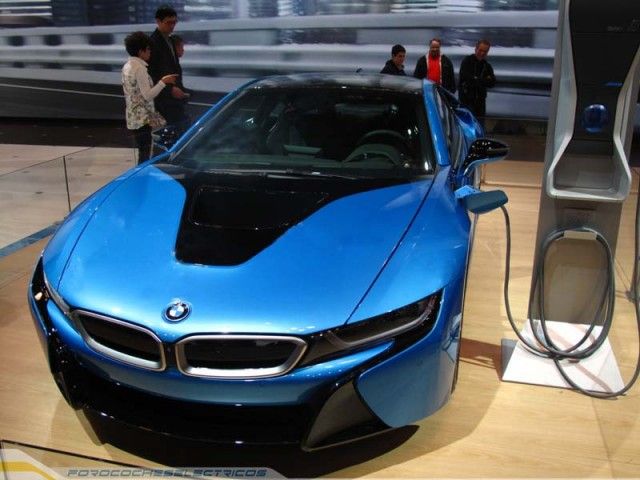
El BMW i8 es mucho más que un deportivo con carácter sostenible. Es un enorme proyecto que ha supuesto explorar nuevos territorios para un fabricante que después de más de 30 años coqueteando con los eléctricos, ha dado el paso definitivo.
Un ejemplo de lo especial de este desafío es el proceso de fabricación de los coches. Un proceso donde la fibra de carbono y la palabra sostenibilidad se dan la mano, para crear un vehículo capaz de moverse muy rápido, pero también con muy poco combustible, y que además es totalmente reciclable.