A la batería de litio aún le queda margen de mejora: nueva tecnología láser que aumenta sus prestaciones
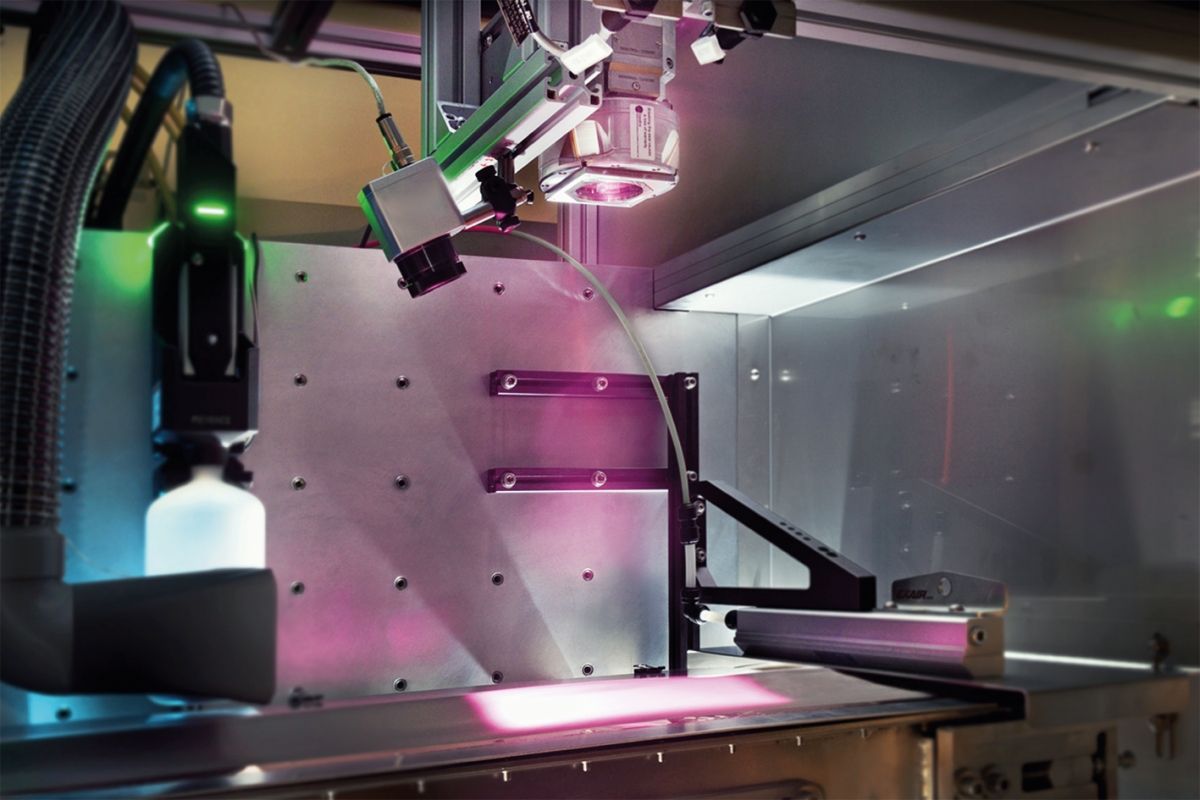
Un equipo de investigadores del Instituto Fraunhofer ha desarrollado tecnologías novedosas que se basan en el uso de láseres para producir baterías de iones de litio. En comparación con las producidas mediante métodos convencionales, tienen una vida útil más larga y pueden cargarse con mayor rapidez.
Las baterías son componentes clave en la movilidad del futuro, tanto en sistemas estacionarios de almacenamiento de energía como en vehículos eléctricos. Por esta razón, los investigadores en todo el mundo están trabajando arduamente para mejorar la tecnología de las baterías.
El Instituto Fraunhofer de Tecnología Láser (ILT) en Aquisgrán ha desarrollado recientemente dos tecnologías innovadoras, basadas en láser, que permiten producir celdas de batería con mayor densidad y con una vida útil más prolongada, al mismo tiempo que se ahorra energía en el proceso de fabricación.
Uno de los aspectos clave en la producción de baterías de iones de litio es la creación de electrodos con grafito. Este proceso implica la aplicación de una pasta de grafito sobre una lámina de cobre, que se seca posteriormente en un horno continuo a una temperatura de 160 a 180 ºC mediante el proceso de rollo a rollo.
A pesar de ser un proceso efectivo a gran escala, estos hornos consumen una gran cantidad de energía y ocupan un espacio significativo, con longitudes de hasta 100 metros y secando hasta 100 metros de lámina por minuto.
Secado con láser de diodo
Los investigadores del Fraunhofer ILT han creado un sistema de secado eficiente que utiliza un láser de diodo en lugar del tradicional proceso de secado por aire caliente.
Este sistema innovador combina un láser de diodo con una longitud de onda de 1 micrómetro y un sistema óptico especial, diseñado en colaboración con el socio industrial Laserline, para iluminar grandes áreas de la lámina de cobre recubierta con grafito.
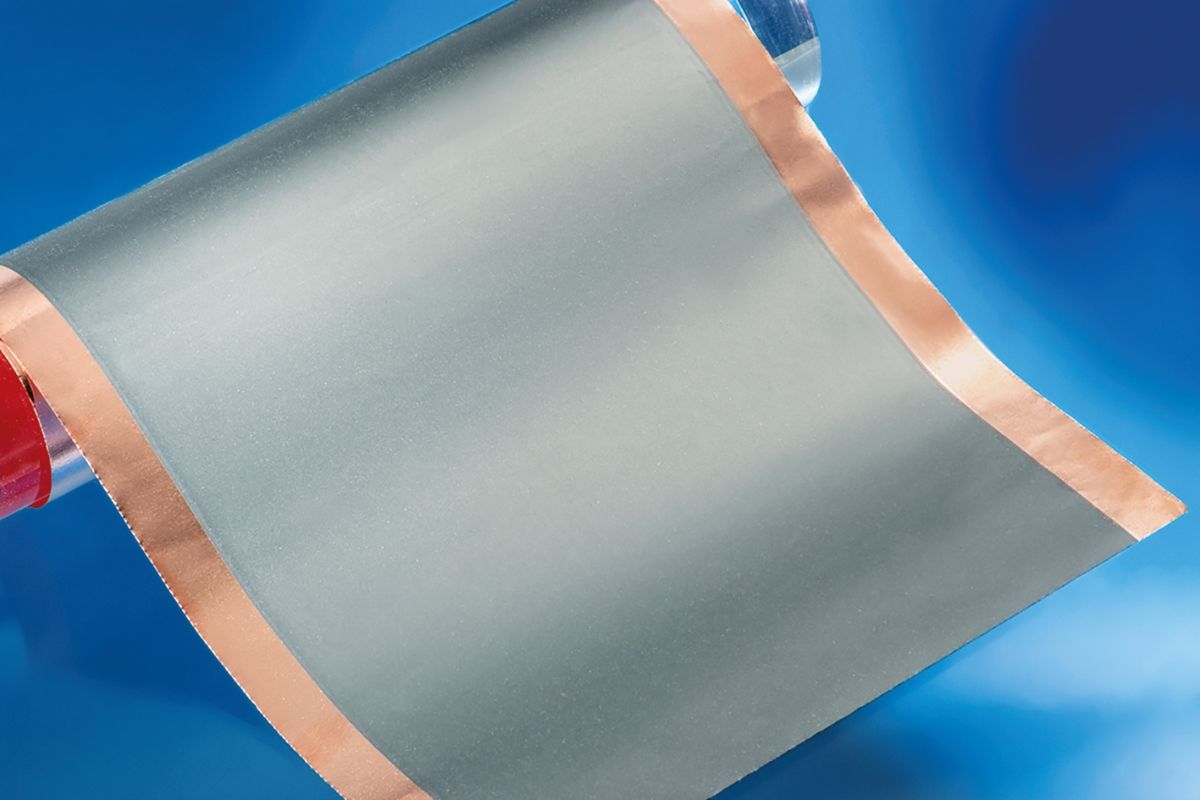
Samuel Fink, gerente de grupo de procesamiento de película delgada en Fraunhofer ILT, explica que el haz de alta intensidad proyectado por el láser de diodo se enfoca en el grafito negro, el cual absorbe la energía y produce el secado.
La tecnología de Fraunhofer tiene muchas ventajas, incluyendo la eficiencia energética en comparación con los hornos convencionales, la reducción del espacio requerido para el sistema de secado, y la emisión de muy poco calor al medio ambiente.
Según Fink, el secado con láser de diodo puede reducir la energía requerida hasta en un 50 % y el espacio necesario para un sistema de secado a escala industrial en al menos un 60 %.
Estructura de electrodos 3D
El equipo de Fraunhofer ILT también ha desarrollado una estructura de electrodos 3D modificada, que mejora la densidad de potencia y la vida útil de servicio de las baterías de iones de litio.
Para lograr esto, han utilizado un láser de pulso ultracorto de alta potencia para crear una estructura de agujeros en el electrodo de la batería, llamados canales, que actúan como autopistas para los iones de litio, reduciendo así la distancia que deben viajar y acortando el proceso de carga.
La principal ventaja de esta tecnología es que permite aumentar el número de ciclos de carga potenciales y prolongar la vida útil de la batería.
El proceso basado en láser y su efecto positivo en la celda de la batería son conocidos en teoría, pero el equipo de Fraunhofer ha logrado transferir estos principios a un proceso escalable y listo para la industria utilizando radiación láser de pulso ultracorto.
Han desarrollado una disposición de haces múltiples para el control de procesos en paralelo, utilizando cuatro escáneres con seis haces cada uno para procesar la cinta en paralelo y cubrir un ancho de 250 milímetros, procesando la capa de grafito de forma continua. Esto permite su uso como proceso de producción digital para mejorar la calidad de las celdas de la batería y aumentar la sostenibilidad durante la fabricación.
Según Matthias Trenn, líder del equipo de estructuración de superficies en Fraunhofer ILT, el siguiente paso es escalar la tecnología desde el prototipo hasta una línea de producción industrial.