La Gigaprensa es una de las claves del éxito de Tesla. Desarrollo de nuevos modelos en 18 o 24 meses y reducción drástica de costes
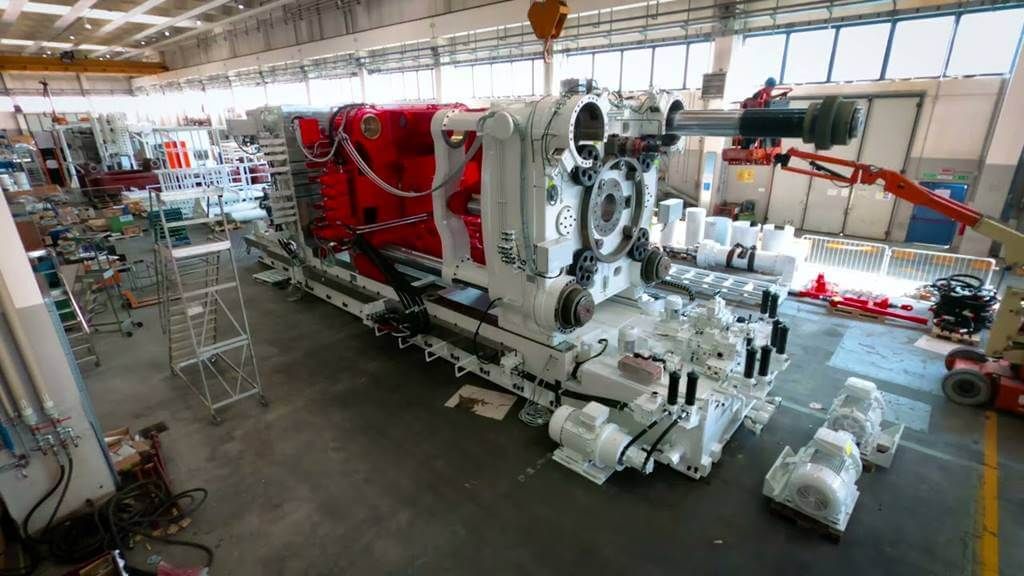
La apuesta de Tesla por el sistema de producción con la denominada Gigaprensa, una prensa de fundición con una enorme capacidad, se ha convertido en una de las decisiones más importantes para el fabricante norteamericano. Una revolución silenciosa que, según los expertos, permite reducir la complejidad, los costes, e incluso reducir los plazos para el desarrollo de nuevas plataformas y modelos.
Así lo indica en un artículo Reuters, que citando hasta cinco fuentes internas de la marca, ha dicho que la tecnología de carrocería de fundición a presión de una pieza de Tesla (gigacasting) ha logrado avances revolucionarios que pueden cambiar el modelo de producción de los coches eléctricos, y ayudar al fabricante americano a lograr el objetivo de reducir a la mitad los costes de producción.
Tesla ha desarrollado una prensa gigante con una presión de entre 6.000 y 9.000 toneladas, que se encarga de fundir integralmente las estructuras de los bastidores delantero y trasero del Model Y o la nueva Cybertruck, reduciendo los costes de producción de forma significativa.
Las fuentes consultadas indican que este avance en la tecnología de carrocerías de fundición a presión de una sola pieza puede fundir aproximadamente 400 piezas usadas hasta ahora en la producción tradicional, y hacerlo en una única pieza.
Los informes dicen que después de que Tesla implemente esta tecnología de carrocería de fundición, el tiempo para desarrollar nuevos modelos se puede acortar a entre 18 y 24 meses. Una cifra extremadamente corta que podemos comparar con los entre 3 y 4 años que se tarda actualmente.
Esto otorgará a Tesla otra ventaja. Y es que además del menor coste, también permite al fabricante contar con la posibilidad de poder modificar su oferta de una forma mucho más ágil, para atender los cambios de gustos entre los consumidores.
También contará con la posibilidad de modificar las actuales plataformas de una forma rápida y muy económica. Por ejemplo, en la actualidad en los procesos convencionales, una vez que se ha fabricado un molde de prueba de metal de gran tamaño para la plataforma, los ajustes de mecanizado durante el proceso de diseño podrían costar hasta 100.000 dólares por intento, y rehacer el molde por completo podría costar 1,5 millones de dólares. Rehacer todo el proceso de diseño de un molde de metal grande normalmente costaría alrededor de 4 millones de dólares.
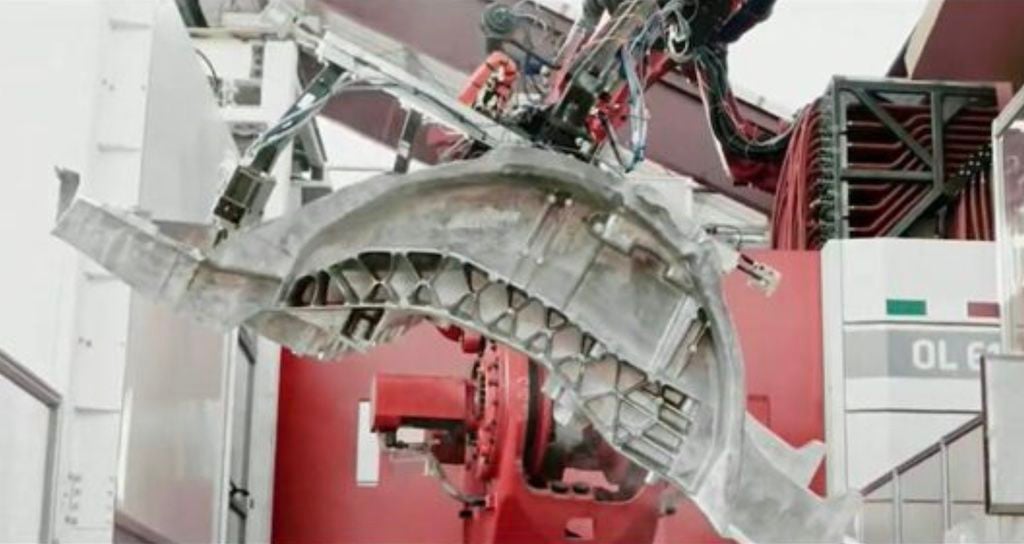
Según las fuentes de Reuters, el coste del proceso de validación del diseño con fundición en arena, incluso con múltiples versiones, es mínimo: solo el 3% de hacer lo mismo con un prototipo de metal.
Eso significa que Tesla puede modificar los prototipos tantas veces como sea necesario, reimprimiendo uno nuevo en cuestión de horas utilizando máquinas de empresas como Desktop Metal (DM.N) y su unidad ExOne.
El ciclo de validación del diseño utilizando fundición en arena solo lleva de dos a tres meses, dijeron dos de las fuentes, en comparación con entre seis meses y un año para los prototipos de moldes metálicos.