Tesla sustituirá la clásica cadena de montaje por una revolucionaria técnica de ensamblaje para fabricar su coche eléctrico de 25.000 dólares
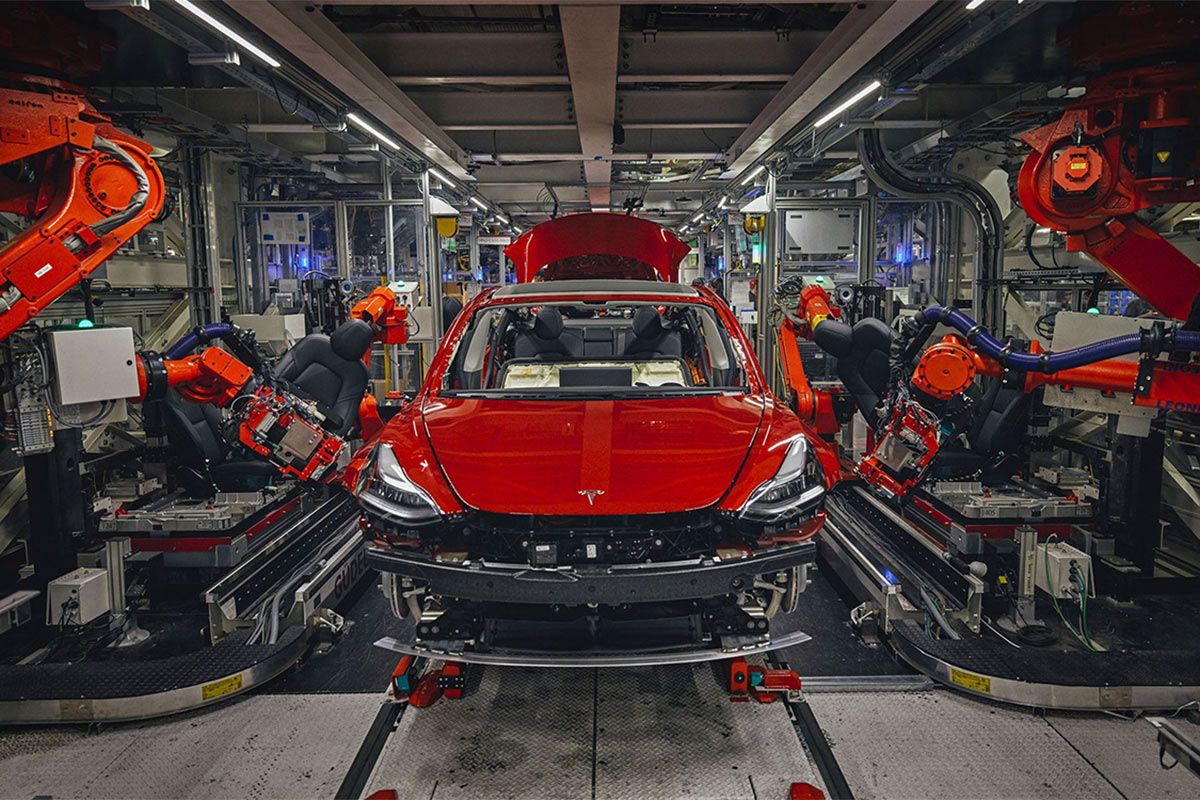
En los últimos años, Tesla ha revolucionado en varias ocasiones los métodos de producción de la industria automotriz. Gracias a avances como el gigacasting, que competidores como Toyota, Volkswagen y Volvo se están apresurando en adoptar, la firma estadounidense ha logrado rebajar de forma notable los costes de fabricación de sus dos productos estrella, los Model 3 y Model Y.
La marca capitaneada por Elon Musk pretende ir un paso más allá con el lanzamiento de su próximo eléctrico de acceso, que tendrá un precio objetivo de 25.000 dólares. En palabras del directivo, “tanto el diseño […] como las técnicas de fabricación están muy por encima de cualquier otra cosa presente en la industria”.
La meta de Tesla es lograr que la plataforma del nuevo modelo, que será un SUV compacto, cueste la mitad que la utilizada en los Model 3 y Model Y. Para conseguirlo, prescindirá de la clásica cadena de montaje que el sector lleva más de un siglo evolucionando desde que Henry Ford la implantara para fabricar en serie el legendario Model T (1908-1927).
Así lo ha confirmado Mathew Vachaparampil, CEO de la empresa consultora de reducción de costes y evaluación comparativa automotriz Caresoft, en una reciente entrevista con Automotive News. La compañía ha dedicado 200.000 horas a construir una réplica digital de la nueva técnica de ensamblaje, bautizada como “unboxed”, la cual consiste en producir diferentes secciones del vehículo al mismo tiempo en áreas distintas de la planta para después juntarlas al final del proceso.
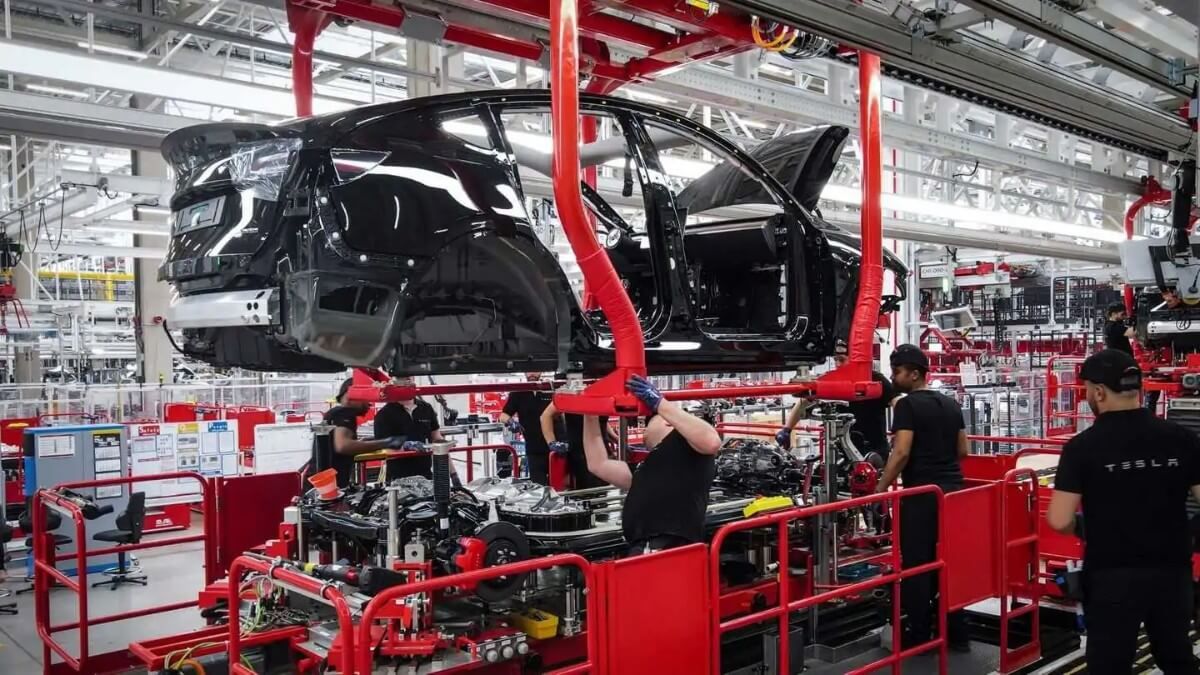
La próxima plataforma eléctrica de Tesla costará la mitad que la utilizada en los Model 3 y Model Y
De acuerdo con las estimaciones preliminares, al evitar que el automóvil recorra una línea de montaje tradicional se acortarán enormemente los tiempos de producción. Además, esta solución también podría requerir un 40% menos de espacio en una factoría.
Por otro lado, Caresoft predice que conllevará una reducción de al menos el 50% en las inversiones en los talleres de pintura (la parte más cara de una planta automotriz), pues sólo se pintarán ciertos paneles en lugar de toda la carrocería.
A pesar de lo interesante de esta propuesta, no debemos perder de vista que Tesla ha experimentado notables problemas a la hora de llevar a la práctica algunos de sus revolucionarios procesos productivos. Sin ir más lejos, la línea original del Model 3 en Fremont, que estaba altamente automatizada, fue un fiasco. Tampoco podemos dejar de mencionar sus dificultades para escalar la fabricación de las celdas 4680 y de la pick-up Cybertruck. ¿Logrará el método de ensamblaje “unboxed” reemplazar a la longeva cadena de montaje? Lo comprobaremos en los próximos años.
Fuente | Automotive News