BMW desarrolla un revolucionario proceso de reciclaje de baterías que le permite cerrar el círculo productivo
BMW ha desarrollado un nuevo sistema de reciclaje de baterías que reduce a la mínima expresión el impacto ambiental y permite dar una nueva vida a los packs cerrando el círculo de la sostenibilidad.
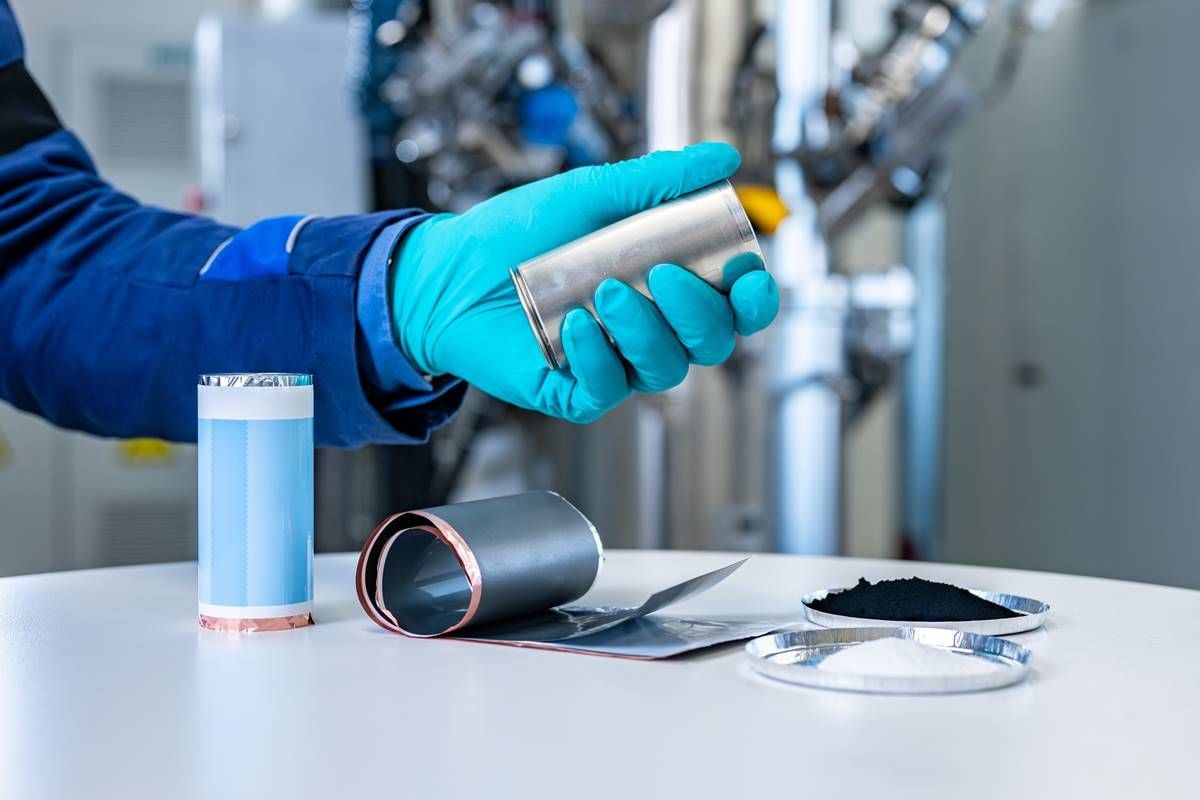
Para lograr con éxito la transformación del transporte a los sistemas eléctricos, reduciendo el impacto ambiental, el reciclaje de las baterías es un aspecto crítico. Los estudios indican que es una cuestión de emisiones, pero también de economía para una Europa fuertemente dependiente en el plano energético y de componentes que dan forma a motores y baterías, y que podrá ahorrar más de 32.000 millones de euros cada año y evitar la emisión de 32.5 millones de toneladas de CO2 a la atmósfera, recuperando los componentes que dan forma a las baterías. Algo en lo que marcas como BMW están trabajando intensamente.
El fabricante bávaro BMW se prepara para construir una nueva fábrica que le permitirá alcanzar un elevado nivel de reciclado y eficiencia en la recuperacon de los componentes que dan forma a las baterías de sus coches eléctricos.
La marca alemana ha desarrollado lo que ha denominado como “un proceso innovador de recuperación y reutilización”. Un método llamado “reciclaje directo” que básicamente supone que las materias primas recuperadas no se devuelven a su estado original, sino que se reintroducen en el ciclo de producción.
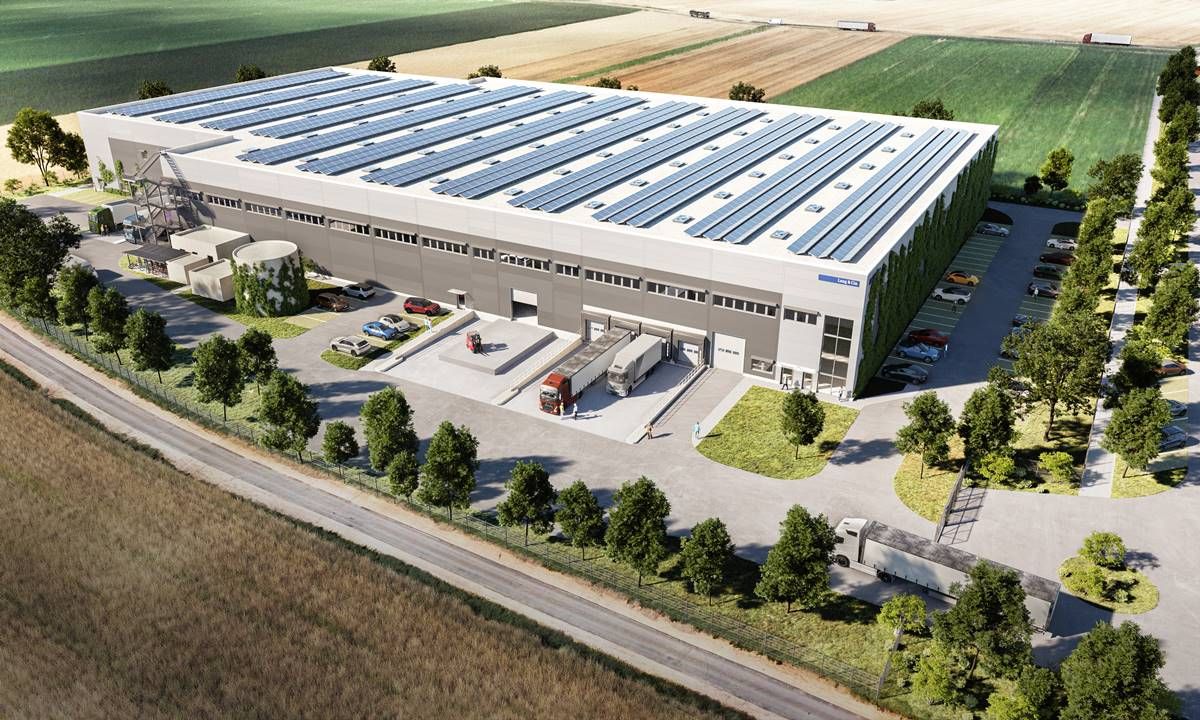
Este proceso evita tratamientos químicos que consumen mucha energía. Esto también permite a BMW acceder fácilmente a materias primas caras como litio, cobalto, grafito, manganeso e incluso níquel. Suficiente para ahorrar dinero, tiempo y emisiones.
El método implica descargar completamente las baterías antes de abrir los pack. Una vez descargadas, los electrodos separan, lo que separa el material activo de las láminas conductoras, que luego pueden regenerarse y procesarse. Luego, los materiales se reintroducen en baterías nuevas. Este proceso innovador se implementará a gran escala en la nueva planta de Kirchroth, en la Baja Baviera.
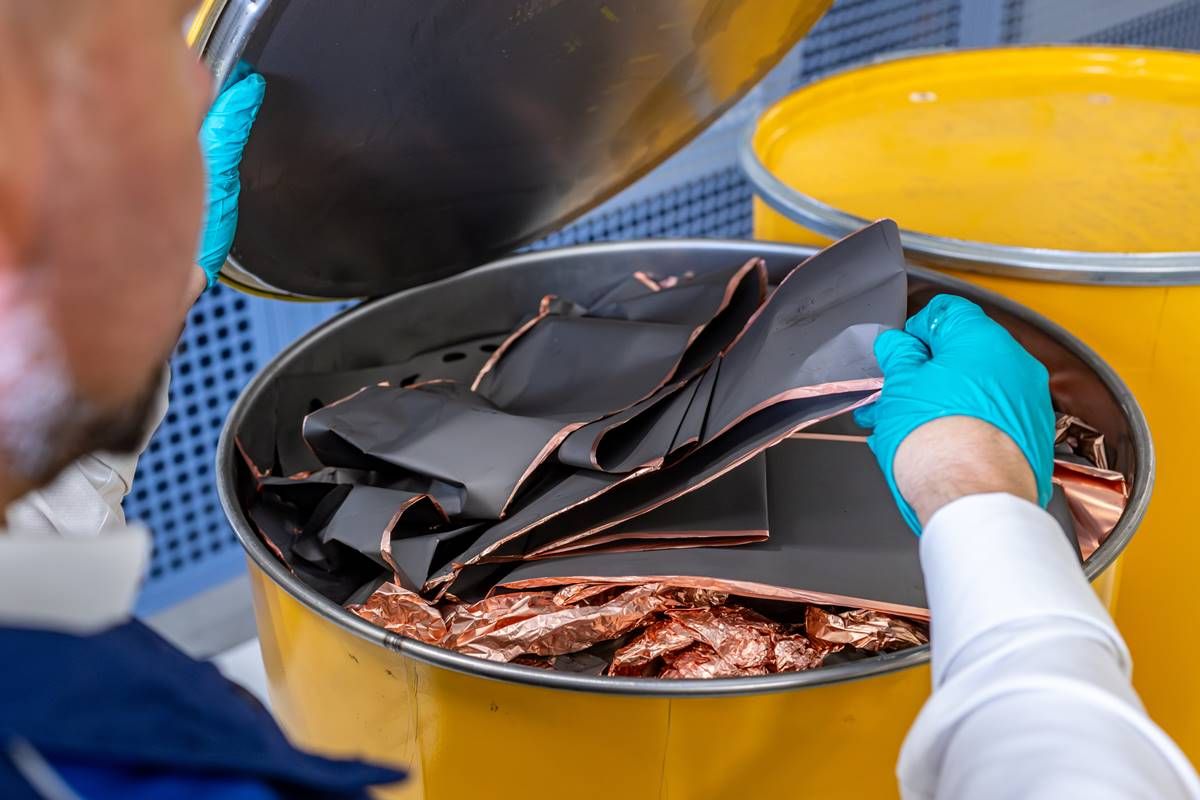
Una inversión de 10,4 millones de euros es el primer paso de un proceso que se expandirá en los próximos años y que permitirá a medio plazo a BMW operar en un circuito cerrado, o al menos reducir de forma drástica la necesidad de adquirir nuevos componentes.
Está previsto que las obras comiencen en la segunda mitad de 2025, y supone un comienzo prometedor y ejemplarizante de que el coche eléctrico es más sostenible, pero puede serlo incluso más todavía si los fabricantes apuestan por el reciclado como herramienta de reducción de costes.