NIO sigue los pasos de Tesla: el eT5 también empleará grandes piezas de fundición en algunas de sus estructuras
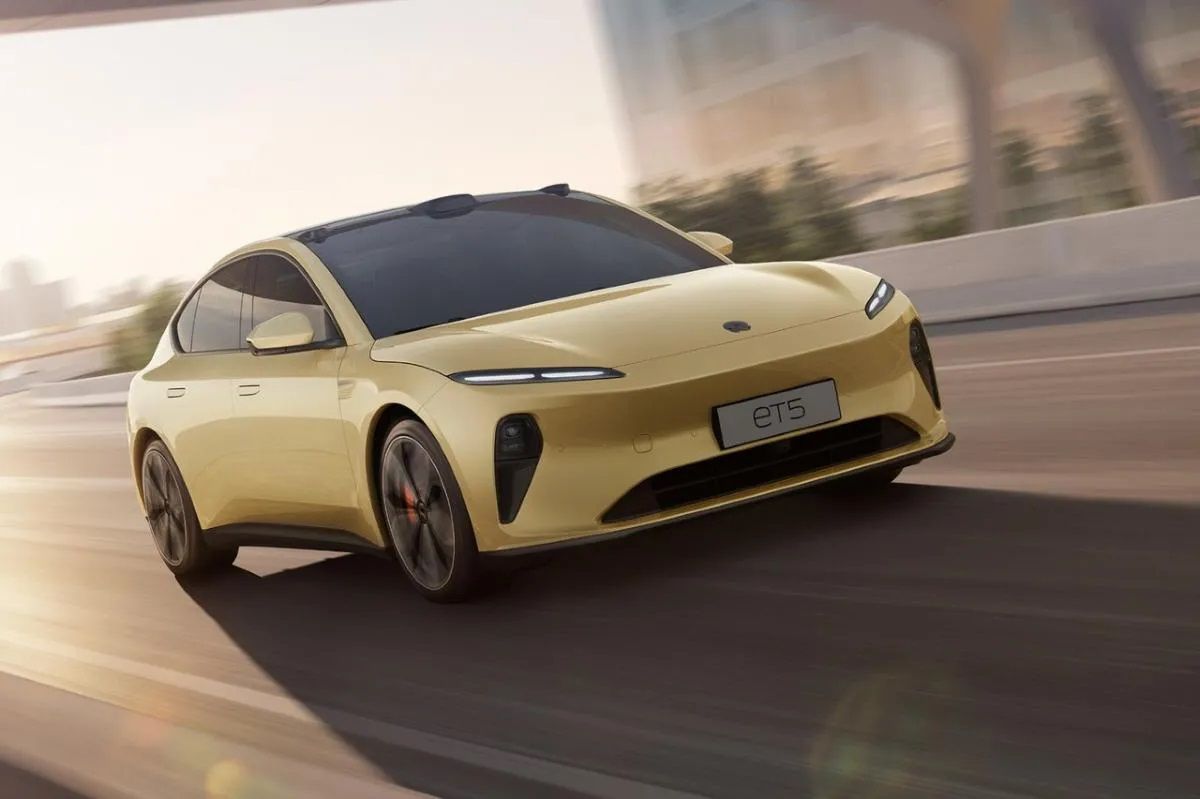
Hace apenas unos días, la marca china NIO presentó el eT5, una avanzada berlina eléctrica de dimensiones similares al Tesla Model 3 que sorprendió a propios y extraños no solo por su vanguardista tecnología, sino por anunciar una autonomía máxima de unos 1.000 km bajo el ciclo de homologación CLTC.
Esto será posible gracias al empleo de unas baterías de 150 kWh de capacidad. Además, también estará disponible con otros dos packs: uno de 75 kWh que le permitirá llegar a los 550 km CLTC, y otro de 100 kWh con el que homologará 700 km CLTC. Por el momento se desconocen las autonomías que lograrán las diferentes versiones bajo el ciclo europeo WLTP.
Dado que el eT5 se venderá en los mercados internacionales, NIO ha hecho especial hincapié en la seguridad del sedán, que combinará un completo arsenal de sensores y cámaras de alta resolución con un potente ordenador ADAM de Nvidia para ofrecer a los usuarios un sistema de conducción autónoma (NAD) de nivel 3.
NIO no solo ha cuidado la seguridad activa de su última creación, sino también la pasiva, pues cuenta con un cuerpo híbrido de acero y aluminio ultra-resistente capaz de ofrecer una rigidez torsional muy elevada. Ahora, la marca ha revelado nuevos detalles de la estructura del vehículo, que utilizará algunas soluciones constructivas ya vistas en el Tesla Model Y.
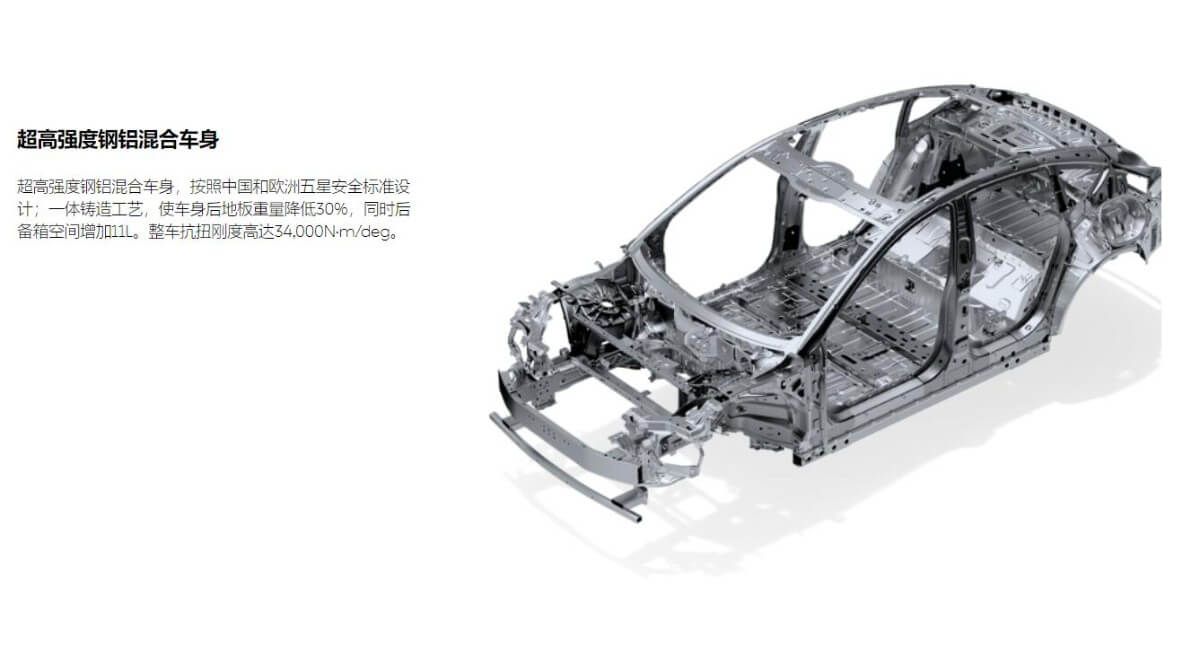
El NIO eT5 ofrecerá hasta 1.000 kilómetros de autonomía
Al igual que el SUV estadounidense, parte del monocasco del NIO eT5 estará construido a partir de grandes piezas de fundición. Frente al uso de piezas de acero estampado soldadas entre sí, este nuevo método permite simplificar, acortar y abaratar el proceso de producción del vehículo, motivo por el que numerosas marcas están decididas a seguir los pasos de Tesla.
En el caso concreto del eT5, NIO ha decidido implementar esta solución en el subchasis trasero, que está realizado en aluminio. En comparación con el proceso de soldadura de acero, esta tecnología permite un aumento de la resistencia de 31.000 Nm/deg a 34.000 Nm/deg, reduciendo además el peso en 13 kg e incrementando el espacio del maletero en 11 litros.
Este método también se emplea en los umbrales de las puertas, reduciendo con ello el peso en 8 kg y mejorando el comportamiento de la pieza en caso de impacto lateral, así como en las pinzas de cuatro pistones utilizadas en los frenos.
Fuente | CnEVPost
Relacionadas | El Deutsche Bank avisa. El NIO ET5 permitirá un crecimiento enorme para el fabricante chino