Ascend Elements producirá desde verano baterías recicladas para coches eléctricos mejores que las de nueva fabricación
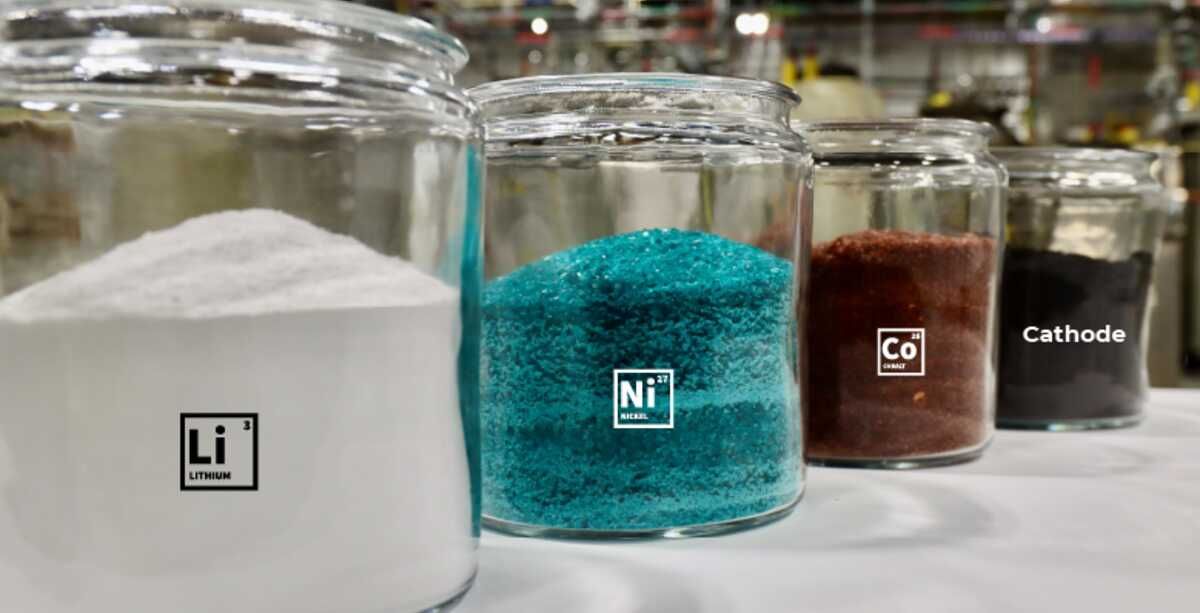
El creciente número de coches eléctricos en las carreteras plantea un problema inmediato y otro en diferido. El primero es que hacen falta muchas cantidades de metales como el litio, cobalto, manganeso y níquel para baterías NMC, y el segundo es que al cabo de unos años habrá que reutilizar y reciclar esas baterías para que no se conviertan en residuos peligrosos.
La economía circular pone solución al problema. Empresas como Ascend Elements (previamente Battery Resourcers) están preparándose para el reciclaje industrial de baterías de litio para recuperar sus componentes y producir nuevas baterías. Hay más de una que hace eso, véase Redwood Materials, pero en este caso el matiz es que sus baterías recicladas resultan ser mejores que las nuevas, un hallazgo imprevisto que se publicó en un paper y que ya ha sido corroborado por pares.
El profesor Yan Wang, del Instituto Politécnico de Worcester (Massachussets, EEUU) comenzó a investigar hace 10 años un proceso de reciclaje de baterías de litio junto a un estudiante de posdoctorado, Eric Gratz. Ambos fundaron Battery Resourcers en 2015, que ha cambiado de nombre hace solo una semana. De las pruebas de laboratorio se pasó a la capacidad industrial reducida para reciclar baterías de litio tanto de coches eléctricos como de residuos de la industria electrónica.
En la primera fase del reciclaje las baterías directamente se mandan a una trituradora sin una separación previa. Tras tamizar los restos en varias pasadas se obtiene la conocida como “pólvora negra”. Mediante un proceso bautizado como “Hidro-a-cátodo™” se transforma el polvillo negro en casi el 100% de los materiales valiosos al eliminar sus impurezas. No queda ningún residuo tóxico.
Mediante un sistema patentado, una combinación de metales van sacando “átomo a átomo” los materiales dentro de la “pólvora negra” en una proporción precisa. La pega del proceso es su lentitud, lleva una semana. El producto resultante, cátodo de batería, se ajusta a las especificaciones de las nuevas unidades recicladas. Como ventajas evidentes está un 93% menos de emisiones en el proceso y a un coste 59% más bajo que con otros métodos como el hidrometalúrgico o el pirometalúrgico.
Y aquí viene la parte interesante. Las baterías recicladas pueden cargar al doble o triple de intensidad, y soportan más ciclos de carga, como un 30% adicional. No solo se disipan las dudas acerca de la calidad de las baterías recicladas, es que se da la vuelta a la tortilla. Para encontrar la explicación hay que irse a nivel molecular, donde está el quid de la cuestión.
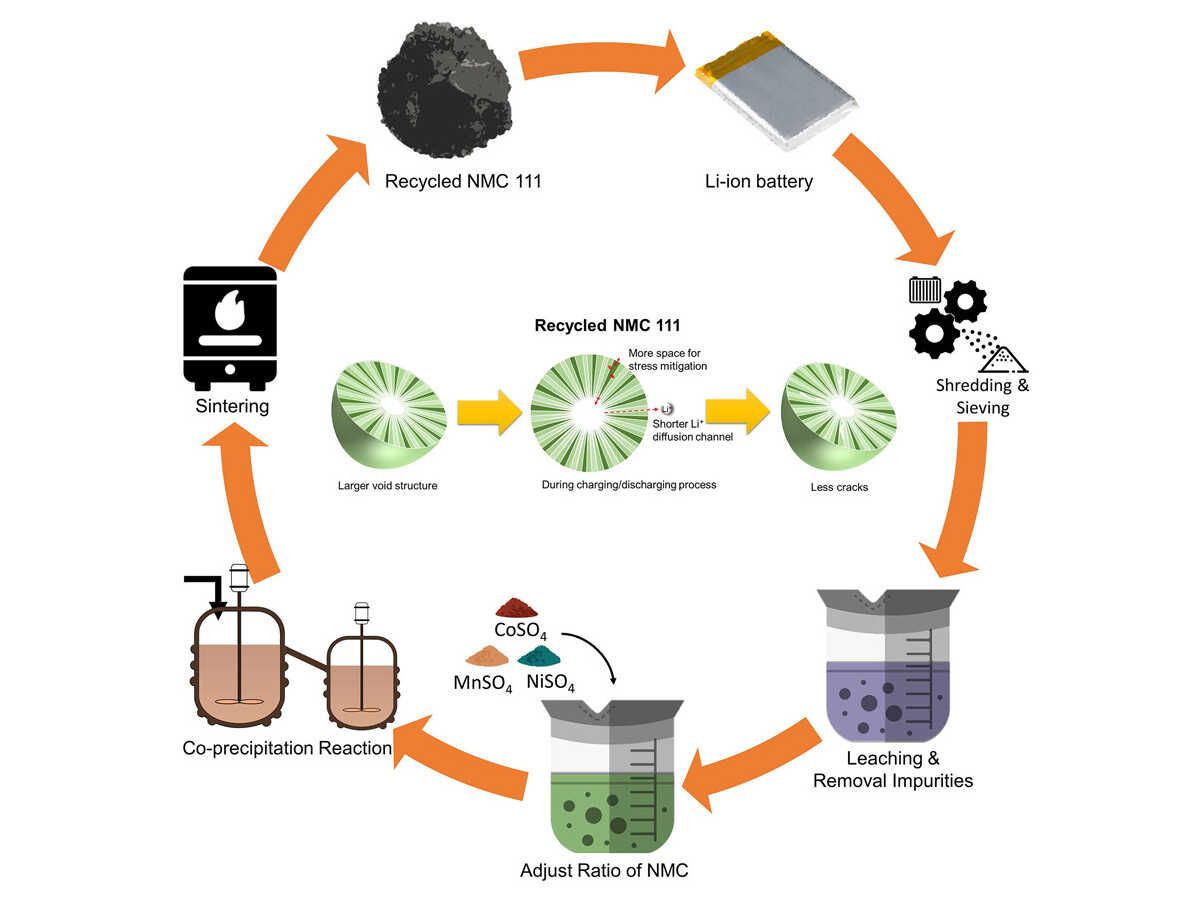
La microestructura de los materiales reciclados contiene “pasillos” o vacíos (mayor porosidad) que resultan en un mejor rendimiento electroquímico. En otras palabras, los iones de litio pueden fluir en ambos sentidos con menor riesgo de colisión, por lo que se reduce la formación de dendritas -estructuras no deseadas que van limitando la capacidad de la batería-.
Si nos vamos al paper publicado -y revisado- en octubre del año pasado, nos cuentan que las celdas de 1 Ah compuestas de LiNi1/3Mn1/3Co1/3O2 (NMC 111) tienen el mejor rendimiento posible de materiales reciclados, con una capacidad restante del 80% con 4.200 ciclos de carga/descarga y el 70% en 11.600 ciclos. Las baterías comerciales con exactamente la misma composición tienen un 33% menos de capacidad con 4.200 ciclos, y un 53% menos con 11.600 ciclos.
El ciclo se puede repetir una y otra vez, reduciendo paulatinamente la necesidad de tirar de terceros países y su industria minera/química
Por lo tanto, el beneficio es doble. No solo se ahorra la minería, transporte, transformación y transporte por varios países del mundo, que implica emisiones y uso de recursos, también se consigue un producto aún mejor, por lo que las ganancias también son importantes. Ascend Elements planea abrir una de las mayores factorías de reciclaje de su país en el Estado de Georgia en agosto este año, actualmente tiene tres plantas piloto de baja escala.

La planta actualmente en construcción tendrá una capacidad de procesar 30.000 toneladas anuales de baterías desechadas. Se ubica en el 9172 de Industrial Drive, en el condado georgiano de Covington. A medio plazo quieren alcanzar una capacidad de 150.000 toneladas anuales con plantas en Europa y Asia.
Ascend Elements tiene un acuerdo con Honda y Jaguar Land Rover. Han conseguido amasar 90 millones de dólares en inversiones, 20 millones en la primera ronda y 70 millones en la segunda; 43 millones se van para su nueva fábrica. Sus baterías recicladas aún no se han incorporado a coches eléctricos, pero han superado pruebas en A123 Systems que demuestran su viabilidad para tal fin.
Vía | WBUR