La impresión 3D llega al coche eléctrico
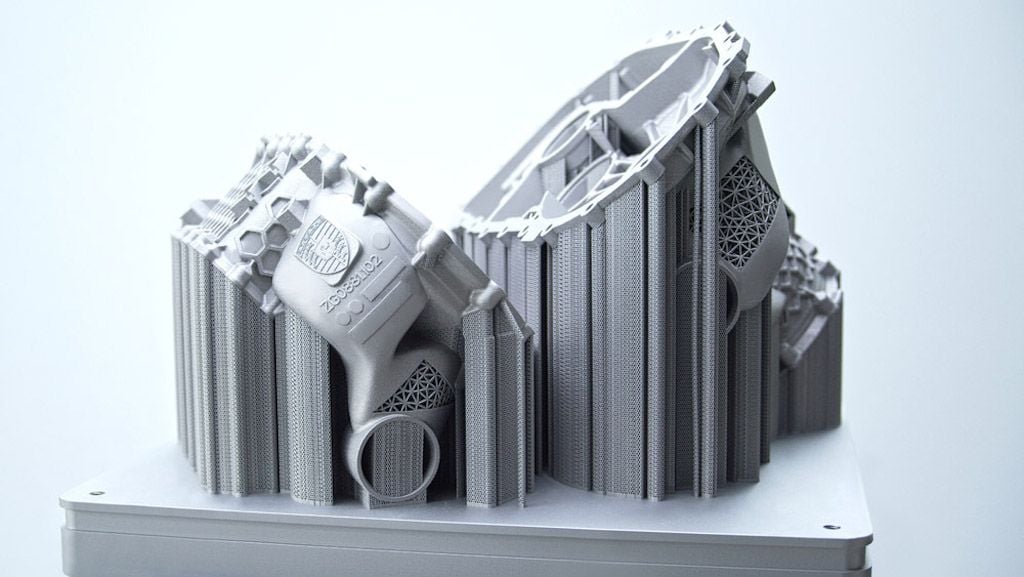
La marca alemana Porsche ha conseguido producir su primera carcasa completa para un accionamiento eléctrico utilizando la tecnología de impresión 3D. La unidad motor-caja de engranajes se ha realizado utilizando un proceso de “fusión láser aditivo“.
Los ingenieros del departamento de Desarrollo Avanzado han logrado realizar una carcasa de aleación fabricada “aditivamente” que resulta ser más ligera que una pieza realizada mediante un proceso de fundición tradicional. Con esta técnica se ha conseguido un peso menor del 10%.
El mejor peso no impide que la rigidez disminuya, de hecho en ciertas áreas que sufren un fuerte estrés se ha duplicado su resistencia.
Otra ventaja de este tipo de fabricación es el hecho de que se pueden integrar numerosas funciones y piezas. Gracias a esto se reduce considerablemente el trabajo de montaje y beneficia directamente la calidad de la pieza.
Una nueva era
Los procesos de impresión 3D abre nuevas oportunidades en el desarrollo y la fabricación de piezas de bajo volumen. Con esta tecnología Porsche está impulsando intensamente el uso de la “fabricación aditiva” para la optimización de piezas altamente estresadas.
El proceso se empleó hace unos meses para realizar nuevos pistones mediante impresión 3D que fueron probados con éxito en un 911 GT2 RS.
En la actualidad no hay otros procesos productivos o de fabricación que ofrezcan tantas posibilidades y una implementación tan rápida como la impresión 3D. Los datos de diseño se pueden enviar a la impresora directamente desde la el ordenador sin pasos intermedios, como hasta ahora ocurría con la fabricación de herramientas y útiles específicos.
Falk Heilfort, uno de los componentes del equipo cuenta el propósito de la prueba: “Nuestro objetivo era desarrollar un accionamiento eléctrico con el potencial de fabricación aditiva, al mismo tiempo que integramos tantas funciones y piezas como fuera posible en la carcasa del accionamiento, ahorrando peso y optimizando la estructura“.
Con la impresora 3D especial utilizada por los ingenieros de Porsche, la impresión del primer prototipo de carcasa llevó varios días y se realizó mediante dos procesos de construcción debido al tamaño de la pieza. En un sector que avanza rápidamente y con las últimas generación de maquinaria específica, es posible reducir este tiempo en un 90%. de esta forma toda la carcasa se puede fabricar en un proceso.
Perfecta para ediciones limitadas
La carcasa producida mediante el proceso de impresión 3D muestra una vez más el potencial de la “fabricación aditiva” para Porsche a la hora de desarrollar productos futuros. este nuevo método de fabricación posee un gran potencial en las áreas de innovación de procesos (para conseguir un desarrollo más ágil y una producción flexible) y para nuevas áreas de negocio como la personalización con nuevas ofertas para clientes, así como para piezas de repuesto específicas.
Esta tecnología de fabricación es técnica y económicamente interesante para la marca alemana, que ve en ella potencial para series especiales y de pequeña tirada, así como para competiciones deportivas.