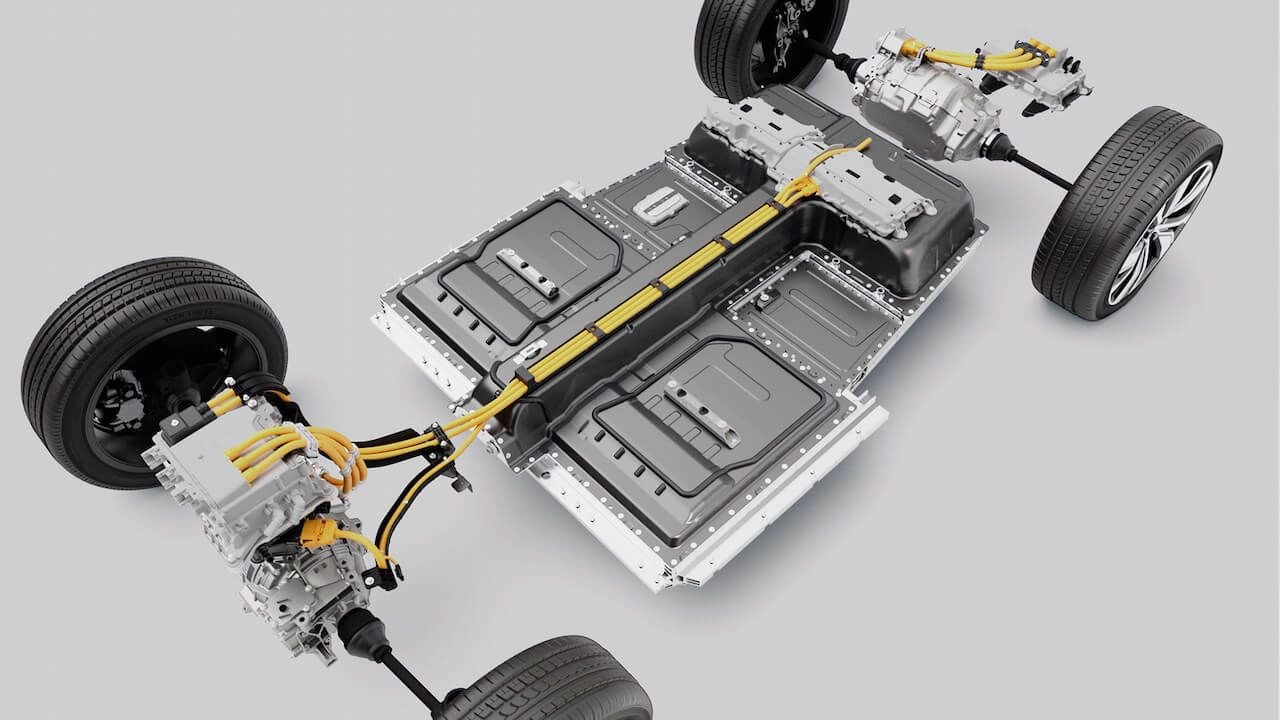
Tesla quiere revolucionar la industria de las baterías: extracción de litio sostenible, uso de silicio en bruto, packs integrados en la estructura de los vehículos…
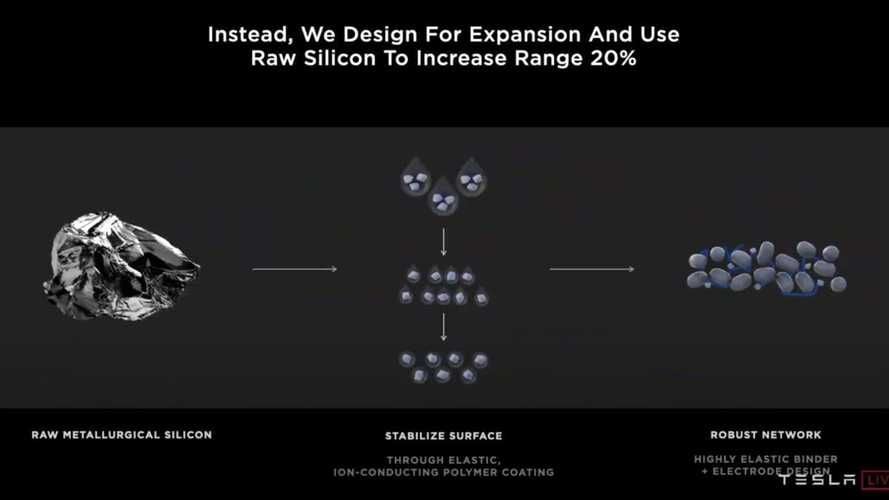
4 min. lectura
Publicado: 23/09/2020 09:23
A pesar de que todos los titulares del «Tesla Battery Day» han sido acaparados por las nuevas celdas 4680 de la compañía, las eficientes Terafábricas, el nuevo coche eléctrico asequible de 25.000 dólares que llegará en 2023 y el prestacional Model S Plaid, estas no han sido todas las novedades que ha presentado la empresa durante el evento.
Uno de los anuncios más interesantes ha sido la confirmación de que Tesla utilizará silicio metalúrgico en los ánodos de sus baterías, algo que permitirá reducir los costes de producción de los packs en un 5% y aumentar la autonomía de sus coches eléctricos en un 20%. Si a esto sumamos otras medidas como el uso de celdas 4680, se logrará una reducción de costes total del 37% por kWh.
Normalmente, el silicio empleado en la industria ha sido altamente procesado mediante costosos tratamientos para que funcione correctamente en diversas aplicaciones. El mayor problema de este material es que sin los tratamientos adecuados tiende a degradarse enormemente cuando se utiliza en baterías de litio. Posiblemente Tesla logre integrar en sus baterías el más barato silicio metalúrgico en bruto estabilizándolo mediante un polímero conductor de iones de bajo coste integrado en el electrodo con un aglutinante altamente elástico.
Por otro lado, Tesla ha comunicado que se introducirá de lleno en el sector de la minería, pues la compañía se ha asegurado los derechos de extracción de un depósito de arcilla de litio de 10.000 acres en Nevada. De acuerdo con Musk, la firma ha logrado desarrollar un nuevo proceso de extracción de litio más sostenible (todos los elementos involucrados serán reutilizables, y el impacto ambiental será mínimo) y asequible utilizando cloruro de sodio. Además, la cercanía de la mina con las plantas de producción de la marca también permitirá lograr una interesante reducción de costes.
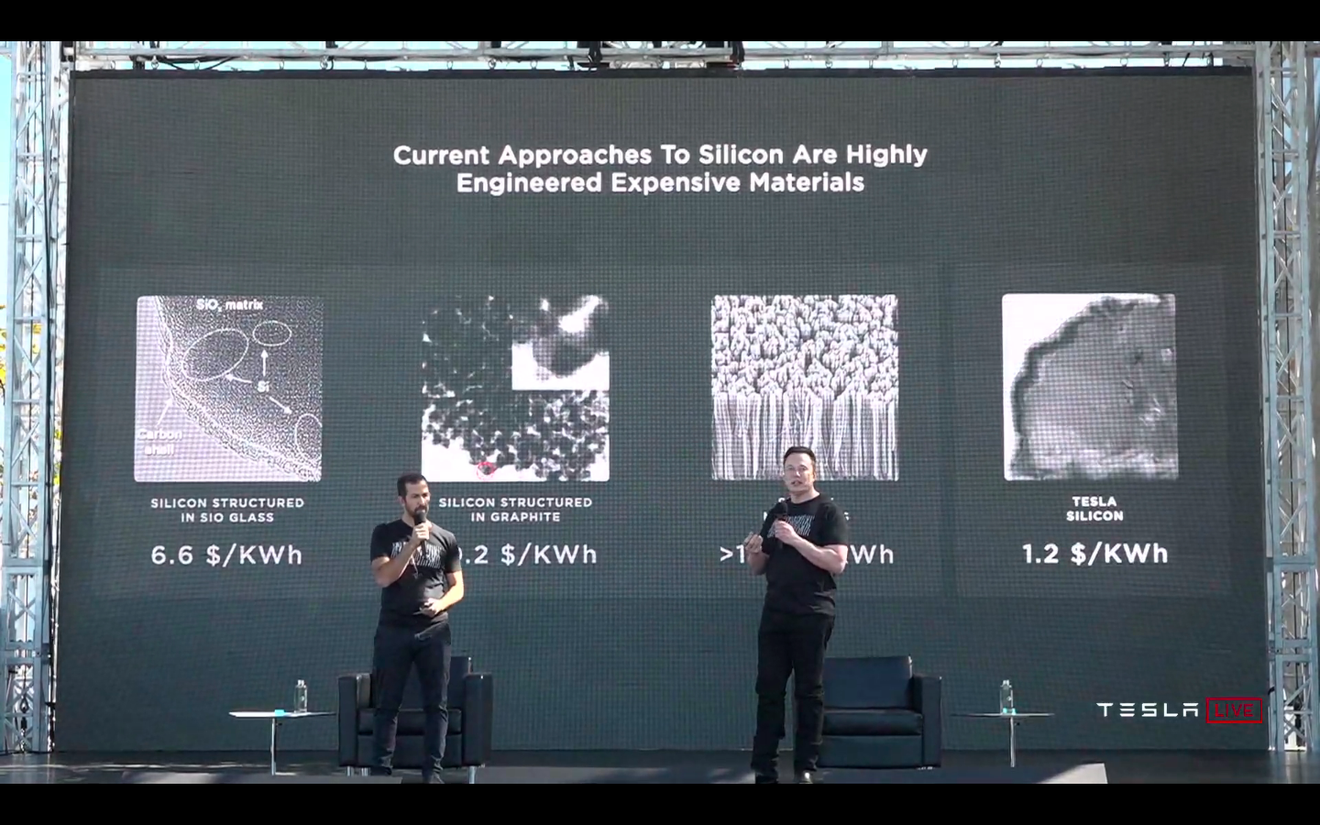
Por último, pero no por ello menos importante, la compañía ha anunciado su intención de integrar los packs de baterías en la estructura de sus vehículos, algo que será posible gracias al proceso de fabricación unibody recientemente estrenado por el Model Y, que permite la creación de grandes piezas de fundición a partir de aleaciones de aluminio muy moldeables y de alta resistencia.
Para finales de año, Tesla ya fabricará el bastidor trasero del Model Y de Fremont a partir de un único bloque (frente a las setenta piezas de acero soldadas entre sí que componen la misma estructura en el Model 3), mientras que el año que viene también se empleará este mismo proceso para producir el bastidor delantero del Model Y de Giga Berlín.
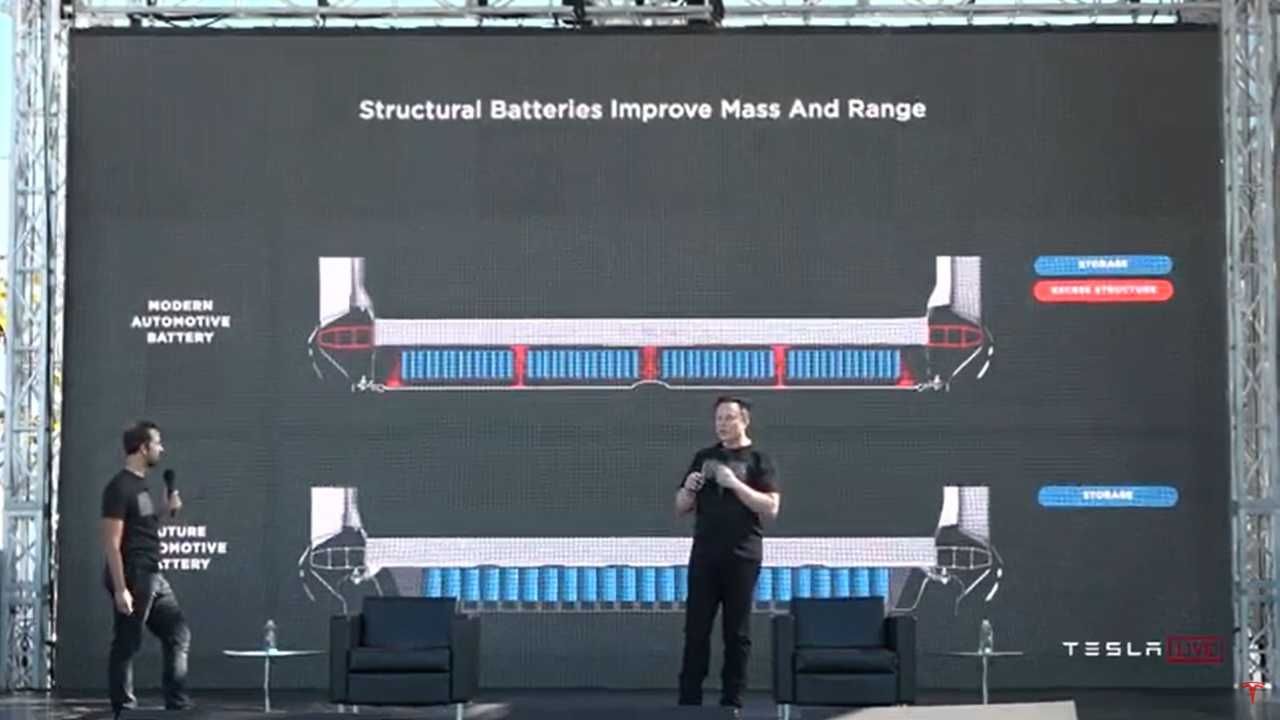
Aparentemente, la intención de Tesla es hacer lo mismo con el bastidor central, el cual además se «fusionará» con el pack de baterías. La empresa denomina esta solución como «batería estructural», pues la propia estructura del vehículo servirá como carcasa de la batería. Su uso permitirá una reducción del peso del 10%, una mejora en la autonomía del 14%, y una simplificación notable del vehículo (se emplearán 370 piezas menos).
De acuerdo con Elon Musk, esta estructura será mucho más rígida que la de cualquier vehículo actual, incluyendo descapotables, lo que redundará en una seguridad pasiva superior y en un mejor comportamiento dinámico. Además, gracias a su simplicidad, esta arquitectura permitirá una reducción de costes apreciable. ¿El mayor inconveniente? Los posibles problemas a la hora de reemplazar las celdas.
Relacionadas | El bastidor frontal del Tesla Model Y fabricado en Alemania estará formado por una única pieza