Tesla produce las primeras celdas 4680 con recubrimiento en seco. Más económicas y más sostenibles
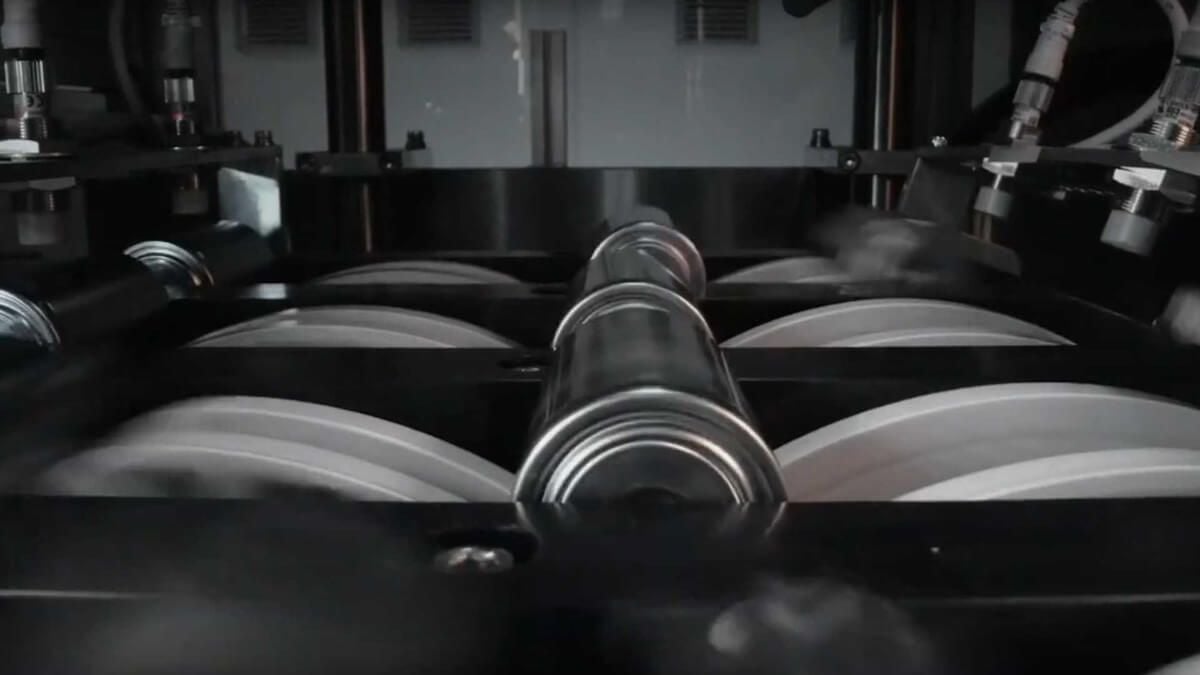
Tesla acaba de cumplir un hito al producir la primera unidad de la Cybertruck dotada de las nuevas celdas 4680 dotadas de recubrimiento en seco. Una tecnología con un enorme potencial que según el fabricante norteamericano, ofrecerá ventajas como la reducción de costes, un proceso de fabricación mucho más sostenible, y la posibilidad de escalar la producción mucho más rápido.
A pesar de que muchos fabricantes están apostando por el electrolito sólido como el futuro, los expertos sitúan a tecnologías como las celdas LFP, el ánodo de silicio o las celdas en hoja como los avances que impulsarán a corto plazo la tecnología.
También se destaca el recubrimiento en seco. Una técnica que apuesta por cubrir el material activo en la parte superior de la lámina de metal para crear el electrodo. En este material activo es donde ocurren las reacciones electro-químicas que permiten que el electrodo almacene energía durante la carga y la libere cuando sea necesario.
Habitualmente, el material activo del electrodo se mezcla con agua o con disolvente orgánico para formar una solución lechosa que, posteriormente, se aplica en la parte superior de dicha lámina. Tras el proceso de recubrimiento, el electrodo se seca y prensa. Este proceso de prensado, conocido en inglés como calendering, permite aumentar la densidad energética del electrodo, ya que se reduce su volumen y su porosidad.
Sin embargo, este proceso de secado requiere mucha energía y tiempo, ya que algunos electrodos pueden tardar hasta 24h en secarse completamente. Además, el disolvente orgánico que se usa durante el proceso es potencialmente peligroso y debe ser tratado para su posterior reutilización.
Beneficios del recubrimiento en seco
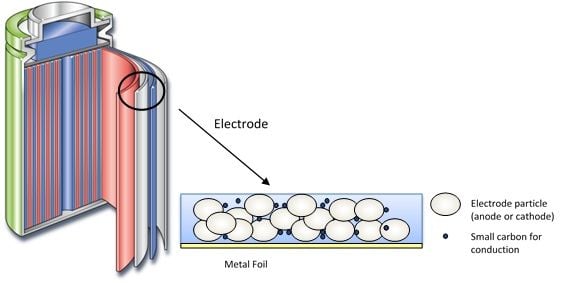
En este nuevo proceso de fabricación por el que está apostando Tesla en su planta de Texas se aplica un pegamento sobre la lámina de metal, fabricado con una mezcla de polvo y ligantes, que sustituye a la mezcla lechosa tradicional. Aunque esta nueva técnica requiere de un proceso de fabricación más complejo, proporciona una reducción significativa de tiempo y costes, además de ser más beneficioso en términos medioambientales.
Al evitar el uso de disolventes, el dry coating requiere menos etapas de preparación y menos equipamiento, lo que implica también una necesidad inferior de capital. Como resultado, un electrodo fabricado con esta nueva técnica tiene una huella de carbono diez veces inferior a la de un electrodo convencional.
Este proceso de fabricación, al ser más rápido y eficiente, permite también una reducción de costes de hasta un 10%. Además, alrededor del 39% de la energía consumida en la fabricación de una batería de iones de litio está asociada a procesos de secado, de los cuales el secado de electrodos supone el 50% de ese gasto energético.
No obstante, la fabricación a gran escala de electrodos empleando esta técnica tiene también sus desventajas. Para que este pegamento sea utilizable, debe ser uniforme en toda la superficie del electrodo. Además, al igual que ocurre con el recubrimiento húmedo, requiere también un proceso de prensado, pero con mayor presión y temperatura.
En el caso de Tesla, en las primeras fases de desarrollo, la mezcla de polvo y ligantes dañó de manera inesperada los rodillos empleados para el prensado de electrodos. Sin embargo, según Elon Musk este es un problema se ha solucionado, lo que ha permitido iniciar la producción de las unidades de verificación.
Si todo marcha como está previsto, Tesla comenzará la producción en serie en el último trimestre de este mismo año, lo que permitirá reducir el coste de fabricación de sus modelos, abriendo el camino al uso en otros modelos, incluyendo su camión Semi.