Este avance permite motores más potentes y baratos sin riesgos térmicos
Un nuevo sensor térmico desarrollado por Continental mide con precisión la temperatura real dentro del rotor de los motores eléctricos. Esto reduce el uso de tierras raras, mejora la eficiencia y permite diseños más compactos. Su impacto técnico e industrial podría ser enorme en la próxima generación de vehículos eléctricos
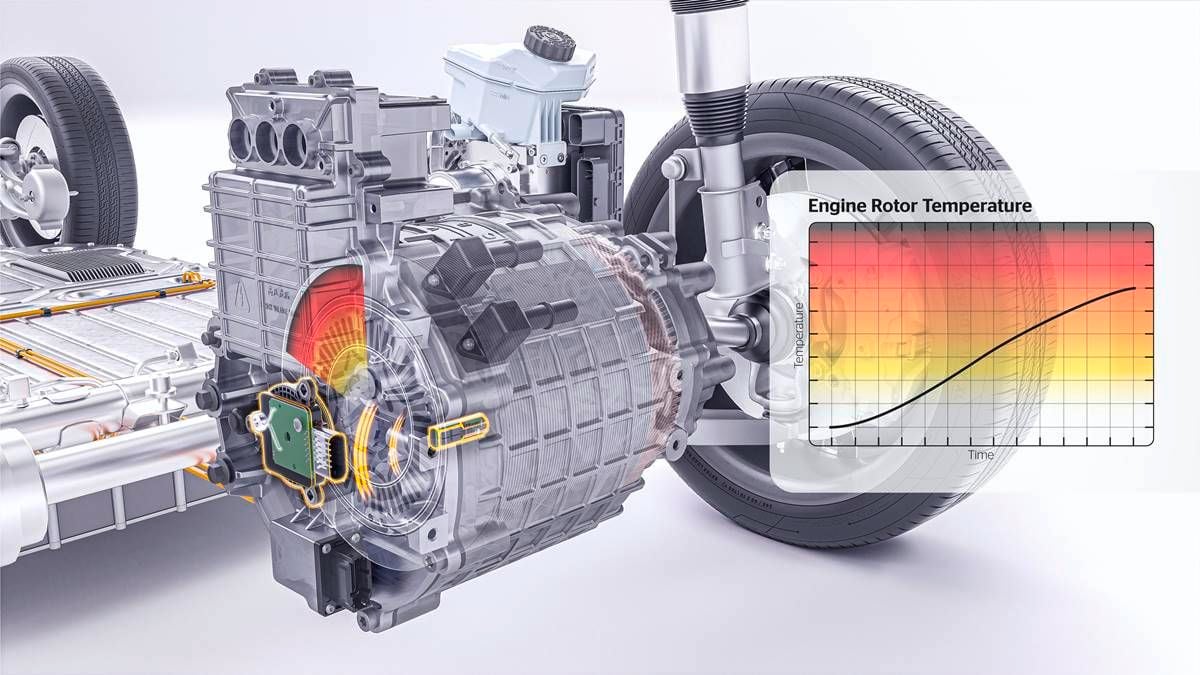
Continental ha presentado una tecnología que, pese a su aparente simplicidad, podría suponer un salto adelante muy importante en el desarrollo de motores eléctricos. Se trata de un micro-sensor capaz de medir directamente la temperatura en el interior del rotor de los motores síncronos de imanes permanentes (PSM), lo que abre la puerta a diseños más eficientes, compactos y sostenibles.
Hasta ahora, conocer con precisión la temperatura del rotor era un desafío. Las soluciones existentes se basaban en modelos de simulación que calculaban esta temperatura de forma indirecta, a partir de variables como la del estator, la intensidad del flujo eléctrico o la temperatura ambiente. El margen de error podía alcanzar hasta 15 °C, obligando a los ingenieros a sobredimensionar componentes clave del motor para evitar riesgos como la desmagnetización de los imanes.
La propuesta de Continental, conocida como eRTS (Embedded Rotor Temperature Sensor), soluciona este problema con un margen de error de solo 3 °C. Este avance permite trabajar mucho más cerca de los límites térmicos del motor sin comprometer su durabilidad, abriendo la puerta a un uso más racional de los materiales, especialmente de las tierras raras.
Tecnología eRTS: cómo funciona
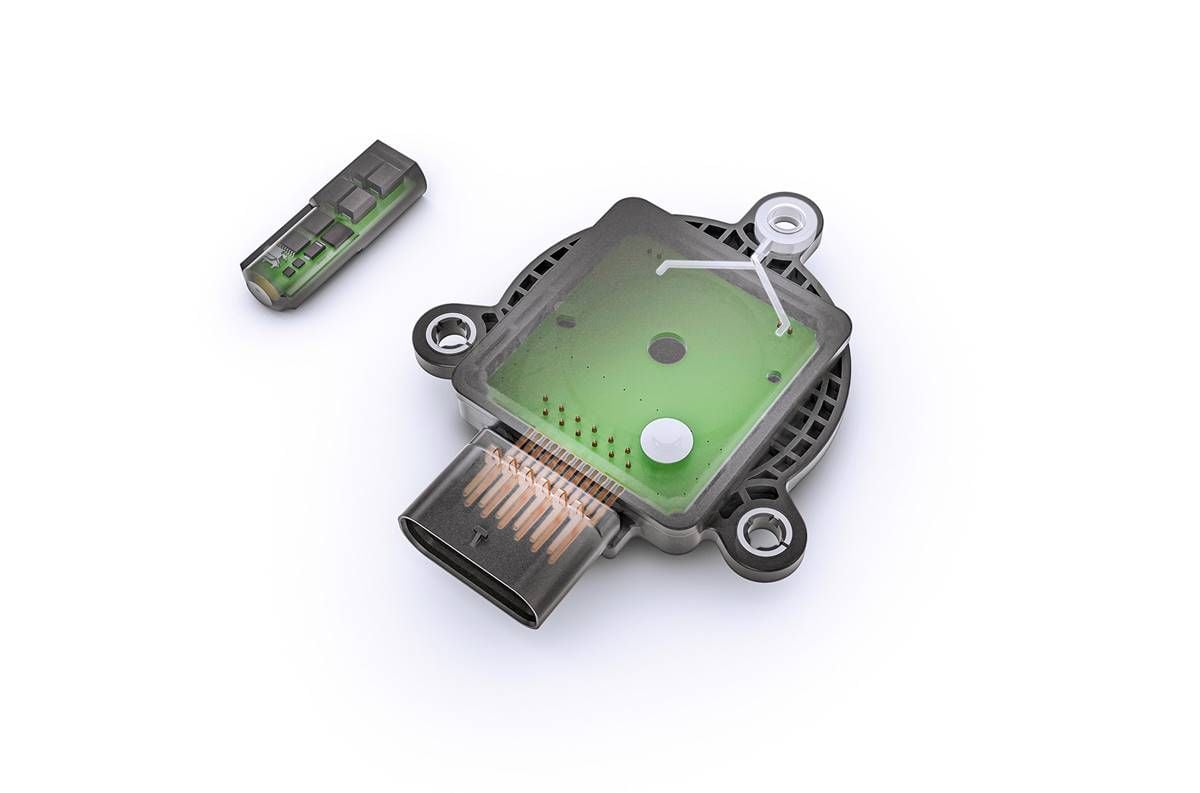
El sistema eRTS está compuesto por dos elementos: un micro-sensor denominado Mote, ubicado directamente junto a los imanes del rotor, y un receptor llamado Transducer, que recopila los datos térmicos y los transmite en tiempo real al controlador del inversor.
Este esquema permite realizar un seguimiento dinámico y preciso de las condiciones térmicas del motor en pleno funcionamiento, algo especialmente útil en escenarios de alta carga o exigencia térmica, como aceleraciones intensas o conducción prolongada a alta velocidad.
Impacto en costes, materiales y sostenibilidad
Una de las grandes ventajas de esta tecnología es su capacidad para reducir la cantidad de tierras raras necesarias en la fabricación del motor. Estos materiales, además de costosos, tienen un importante peso geopolítico y su extracción plantea problemas medioambientales. Con una medición más precisa de las temperaturas internas, los fabricantes podrán ajustar mejor la composición de los imanes, abaratando costes y reduciendo la huella ecológica.
Además, al mejorar la gestión térmica, el diseño de los motores eléctricos podrá optimizarse aún más, permitiendo configuraciones más potentes sin necesidad de aumentar volumen ni peso. También se espera una mejora en la fiabilidad y una disminución del consumo energético del sistema de refrigeración.
Un paso adelante en la industrialización del coche eléctrico
Más allá del componente técnico, esta innovación tiene implicaciones industriales claras. Supone un avance clave en la eficiencia de producción de sistemas motopropulsores eléctricos, lo que beneficia tanto a fabricantes como a proveedores. En un mercado en plena expansión como el del vehículo eléctrico, este tipo de desarrollos podrían marcar la diferencia entre liderar o seguir al resto.
Fuente | Continental