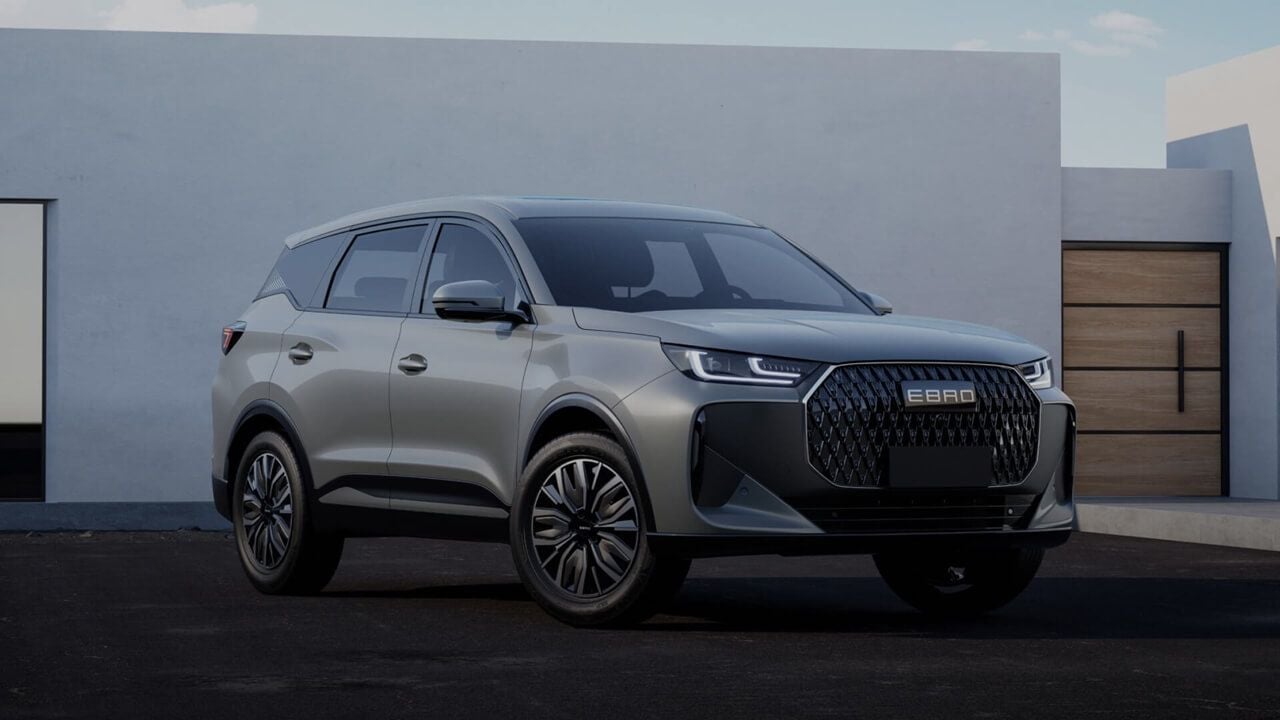
¿Ha conseguido el BMW i3 popularizar la fibra de carbono en el automóvil tras más de 150.000 unidades vendidas?
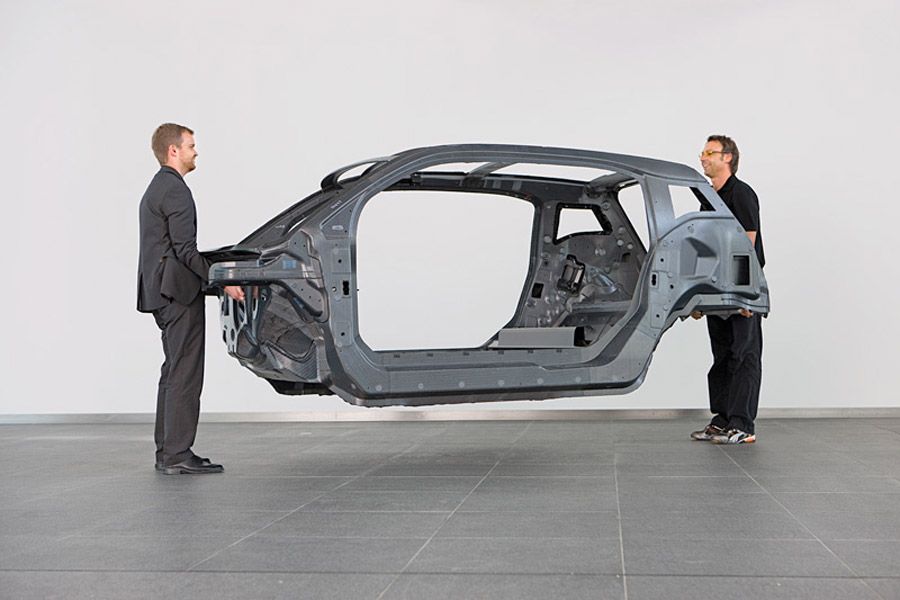
4 min. lectura
Publicado: 06/05/2019 12:30
Cuando el BMW i3 fue lanzado al mercado hace seis años, fue una propuesta sorprendente a varios niveles. El primer coche eléctrico de producción masiva de BMW contaba con soluciones llamativas como una versión dotada de extensor de autonomía de gasolina (i3 REx), puertas traseras con apertura suicida… y una avanzada estructura de fibra de carbono.
Así, el BMW i3 se convirtió en el primer coche medianamente asequible dotado de un monocasco de fibra de carbono. Este material, utilizado en los coches de competición de Fórmula 1 y en superdeportivos como el Lamborghini Aventador, tiene una resistencia superior a la del acero a pesar de ser más ligero que el aluminio, lo que permite crear coches muy seguros y con una rigidez estructural superlativa, pero con un peso muy contenido, algo esencial para lograr unas mejores prestaciones y unas cifras de eficiencia optimizadas.
El principal problema de este material es lo caro y complejo que resulta de fabricar, por lo que el hito conseguido por el i3 es realmente destacado. A pesar de que ni su precio de algo más de 38.000 euros ni sus cifras de ventas (poco más de 150.000 unidades desde 2013) son los de un coche verdaderamente popular, lo cierto es que es el primer automóvil de la historia con un monocasco de fibra de carbono en lograr unas cifras tan masivas.
Con todo, recientemente BMW indicó que tras la desaparición del i3 la década que viene, dejarán de producir monocascos de fibra de carbono, por lo menos en coches de gran tirada. Esta decisión se debe principalmente al hecho de que con las baterías de nueva generación, más capaces que las que había disponibles hace unos años, se pueden conseguir autonomías competitivas sin necesidad de recurrir a materiales de coste elevado que permitan reducir el peso de los vehículos.
La marca bávara parece centrada actualmente en el desarrollo de estructuras «Carbon Core», las cuales utilizan acero de alta resistencia, aluminio y fibra de carbono en lugares estratégicos para contener el peso y mantener los costes de producción a raya. Esta solución ya está siendo actualmente empleada en los modelos Serie 5 y Serie 7 de la firma.
Sin embargo, no parece que esta vaya a ser la última palabra de la fibra de carbono en la industria del automóvil. Recientemente, General Motors anunció el lanzamiento de sus cajas CarbonPro para sus modelos pick-up. Si bien estas estructuras, más ligeras y capaces, sólo se ofrecerán en las versiones más caras de la GMC Sierra, según los costes de fabricación se vayan reduciendo en paralelo al aumento de la producción gracias a la economía de escala, su presencia en la gama del pick-up americano podría ir incrementándose.
Es muy posible que en los próximos años sigan desarrollándose nuevos procesos de producción de monocascos de fibra de carbono más sencillos y menos costosos que permitan el lanzamiento de coches más ligeros y seguros, con un mayor aprovechamiento del espacio interior y unas mejores prestaciones y autonomía gracias a una eficiencia optimizada.