LG da un paso más en el desarrollo del recubrimiento en seco de las baterías y adelanta a los fabricantes chinos
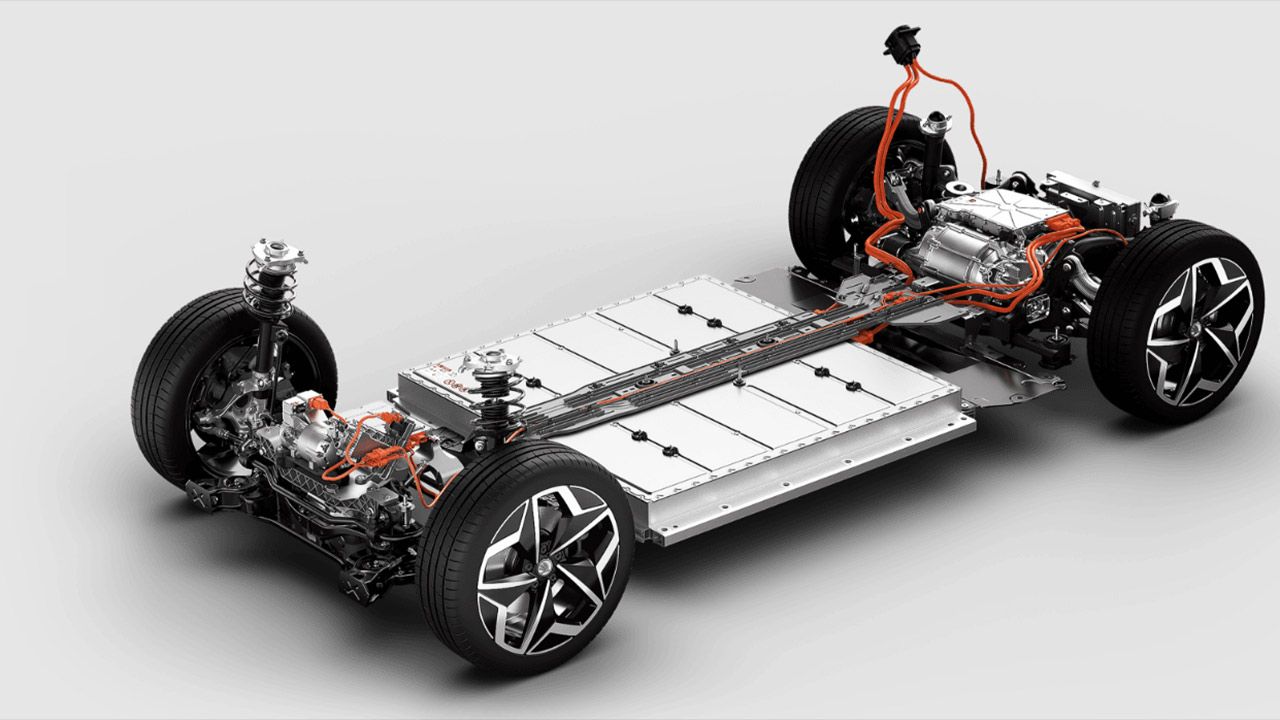
Cuando hablamos del futuro de las baterías para coches eléctricos, se nos llena la boca cuando nos referimos a las ya famosas baterías de estado sólido. Estas recurren, a diferencia de las más habituales de estado líquido, a materiales sólidos para facilitar el flujo de iones entre los electrodos. Estas baterías ofrecen una mejor densidad energética y son más seguras, entre otras ventajas.
Sin embargo, para referirnos a los futuros avances que hagan las baterías más asequibles para el consumidor, también debemos pensar en los procesos de producción. Fíjate en cómo Tesla ha logrado ser la marca número uno en los últimos años en el mercado de coches eléctricos: ofreciendo sus coches a precios más competitivos, gracias en parte a sacarle todo el partido a su método de producción ‘Gigacasting’.
En el apartado de las baterías y su fabricación, llevamos también años hablando de la tecnología de recubrimiento seco. Ahora, la compañía surcoreana LG, en un esfuerzo titánico por hacer frente a la competencia cada vez mayor de los fabricantes chinos (CATL y BYD, especialmente), ha desvelado sus últimos avances para este método de producción de los ánodos y cátodos de las baterías, y que trae una alternativa al proceso húmedo.
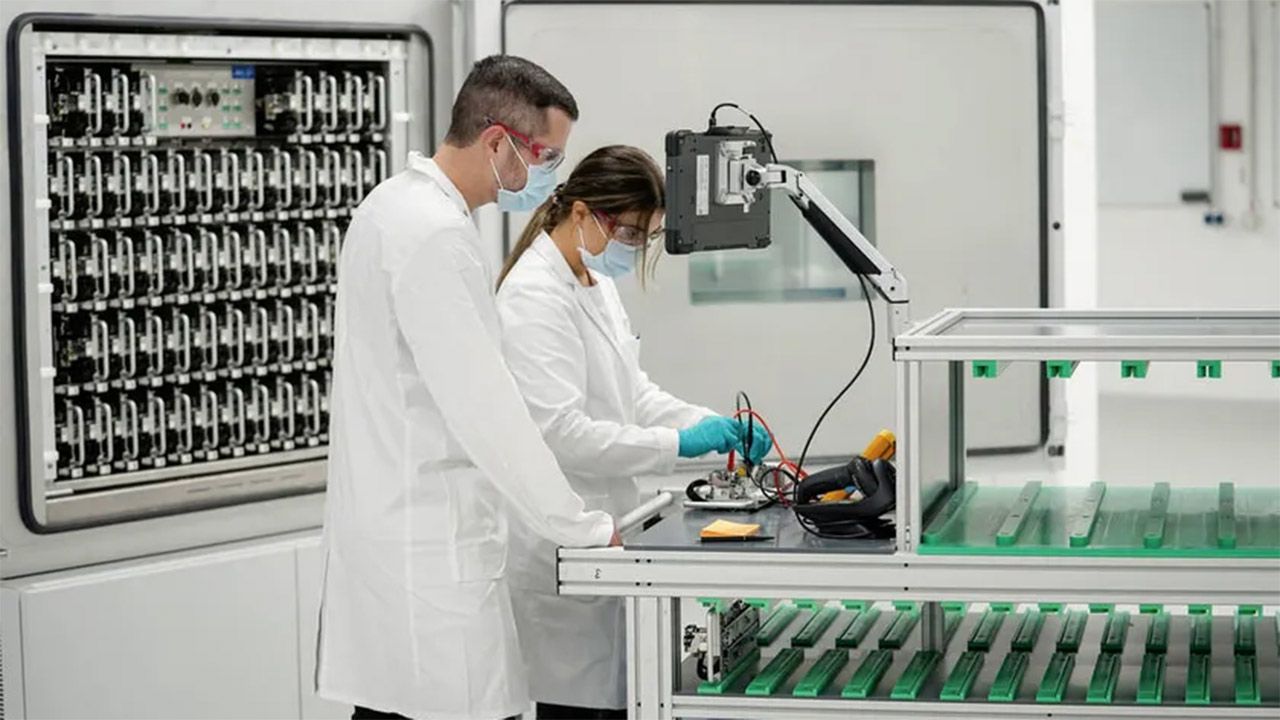
LG Energy Solution pone hasta fecha de llegada para sus baterías fabricadas a base de tecnología de recubrimiento en seco: 2028. A finales de este mismo año comenzará con una línea de producción piloto y para dentro de cuatro años se espera que empiecen a producirla a gran escala. Se trata de buscar y encontrar una fórmula más barata y respetuosa de fabricar dos de los tres componentes clave de la batería, electrolito aparte.
«La tecnología de LG es la mejor entre los competidores, empezamos con ella hace 10 años», aseguró Kim Je-Young, director de tecnología de la firma surcoreana, a la par que estimó que gracias a estos avances pueden reducir los costes de fabricación de baterías entre un 17 y un 30%. El Grupo Volkswagen, como Tesla, Samsung y compañía, llevan años también trabajando en una fórmula de producción que enfrenta varios retos, pero que para ellos supone un «cambio de paradigma».
Según los alemanes, el recubrimiento en seco supondría usar un 30% menos de energía y un 50% menos de espacio en los procesos de producción. A diferencia de esta, el recubrimiento húmedo requiere tanto pasos más costosos como de consumo de más energía para disolver productos químicos en solventes tóxicos, los cuales deben secarse en hornos de casi 100 metros de largo. El recubrimiento en seco evita precisamente invertir en hornos de secado ni en sistemas de recuperación de disolventes, por lo que se requieren menos etapas de preparación, menos equipamiento y menos inversión.
A diferencia de Tesla, que encontró grandes dificultades en los últimos años con esta tecnología, LG ha logrado desarrollar el recubrimiento en seco tanto para ánodos como para los cátodos (Elon Musk no encontró la fórmula para esto último). El reto en esta tecnología reside en que el procesamiento en seco del cátodo es más completado porque estos tienden a estar fabricados en materiales más difíciles de manipular. Precisamente Tesla solicitó ayuda a LG para solucionar los retos de sus problemáticas celdas 4680.
«La industria de los coches eléctricos está considerando formas de producción diferentes. Existe demanda de una forma de producción totalmente diferente para vencer a los rivales chinos», comenta Jang Dong-Won, director ejecutivo de Narae Nanotech, otra empresa surcoreana que suministra recubrimientos para baterías de productos de Apple, claro que Narae está intentando mejorar el proceso húmedo.
Fuente | Reuters