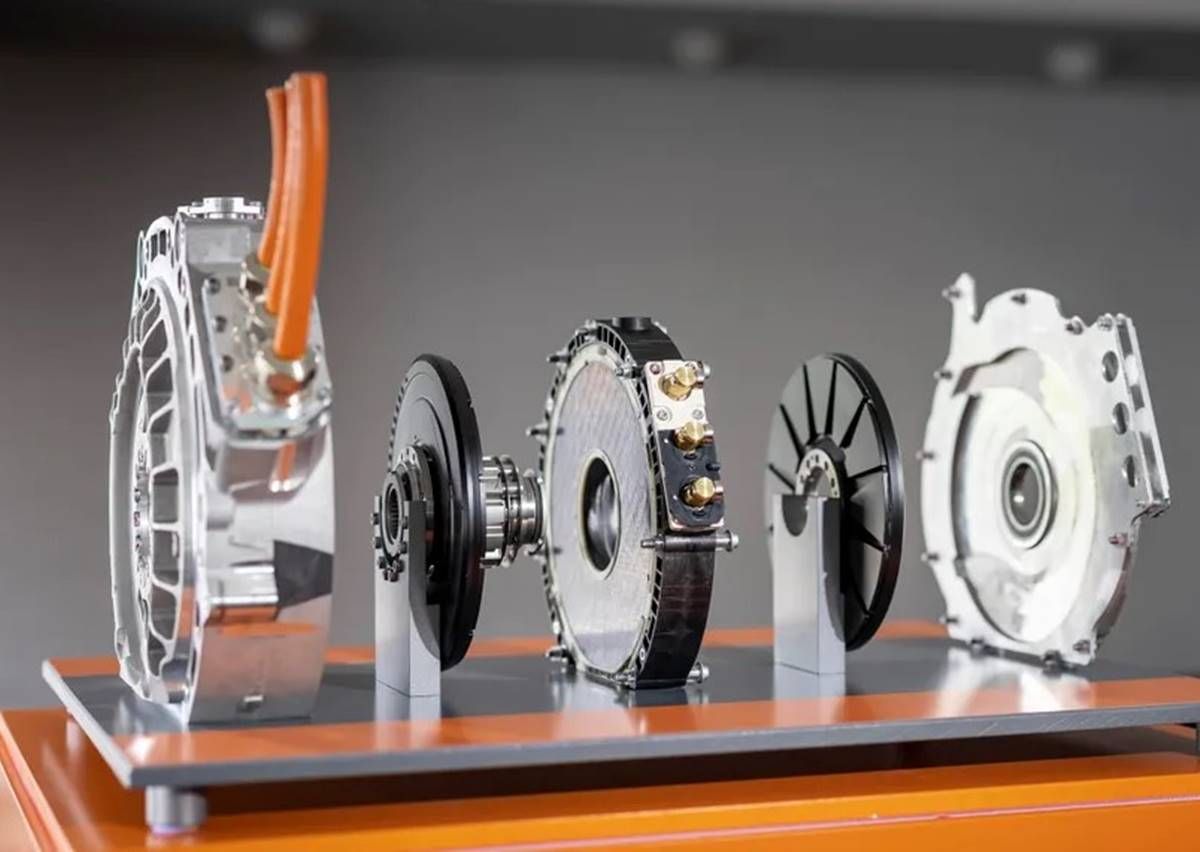
Un 90% más barato y más eficiente. Así es el motor eléctrico que prescinde de tierras raras
Una nueva generación de motores eléctricos flujo axial elimina la necesidad de tierras raras utilizando imanes de hierro. Su diseño compacto y su proceso de producción automatizado los posicionan como solución eficiente para maquinaria ligera y vehículos eléctricos de pequeño tamaño. Una opción estratégica frente a la dependencia de recursos críticos.
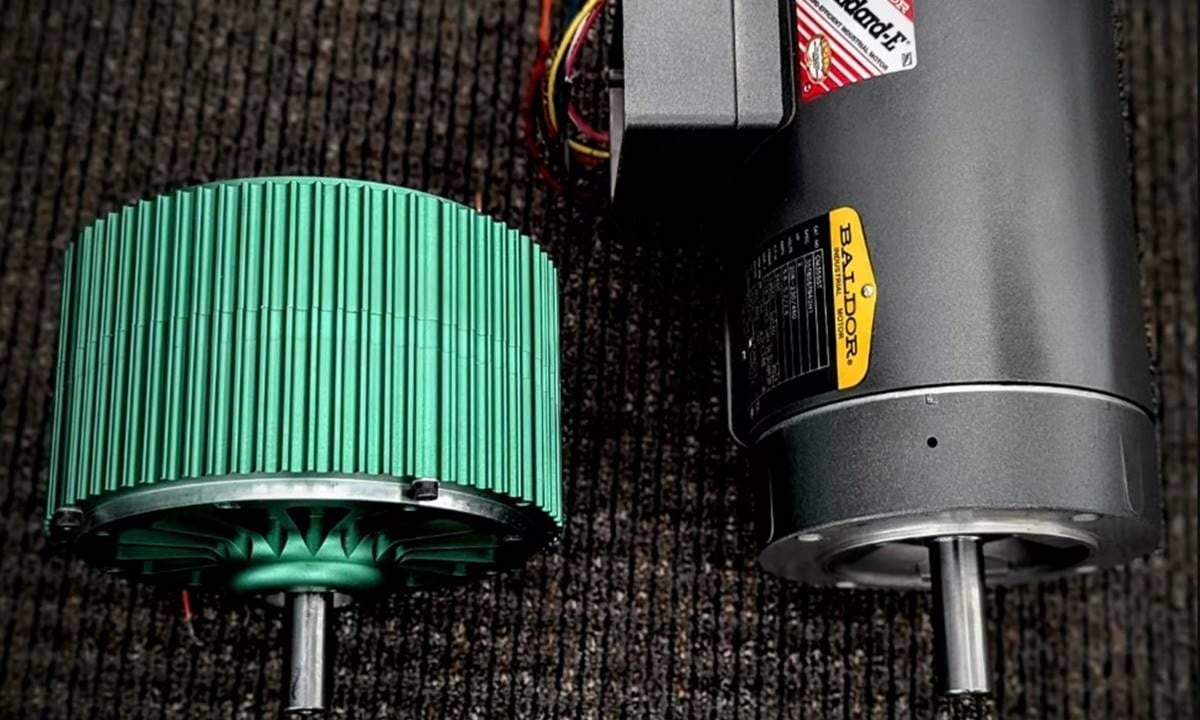
El dominio de las tierras raras en la fabricación de motores eléctricos es uno de los principales cuellos de botella estratégicos para la industria global. Más del 90% del suministro mundial de elementos como neodimio, disprosio o terbio está controlado por China, lo que convierte a estos materiales en vectores geopolíticos críticos. Frente a esta dependencia, se está consolidando una vía tecnológica alternativa: el uso de imanes de ferrita (hierro) en combinación con diseños de motor flujo axial, capaces de ofrecer soluciones competitivas en aplicaciones de potencia contenida.
Diseño flujo axial y bobinado plano: eficiencia y escalabilidad
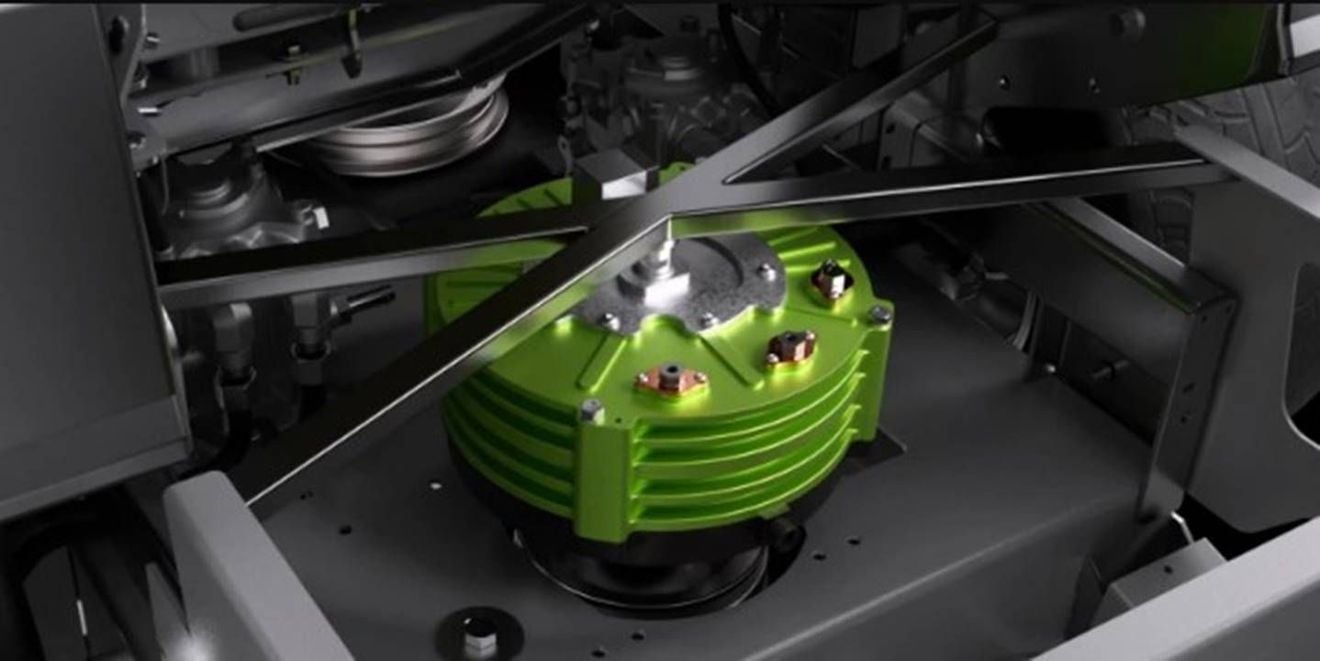
El concepto flujo axial no es nuevo. Desde el siglo XIX ha sido explorado en múltiples configuraciones. A diferencia del motor flujo radial convencional, donde los imanes giran alrededor de un eje central dentro de una carcasa cilíndrica, el diseño axial dispone los elementos magnéticos en discos planos, enfrentados axialmente. Esta arquitectura reduce el camino magnético, aumenta el par motor y mejora el rendimiento volumétrico en aplicaciones de baja a media potencia.
El reto histórico de esta tipología siempre ha estado en la refrigeración y la fabricación. Hoy, gracias a técnicas como la mecanización CNC, el uso de materiales compuestos y los controladores electrónicos avanzados, estos obstáculos se han minimizado. Además, una innovación clave radica en la implementación de un sistema de bobinado plano y multicapa desarrollado por la empresa norteamericana Conifer, inspirado en el apilado de celdas de batería, permite automatizar la producción, reducir los costes del estator en un 90% y escalar sin necesidad de reconfigurar líneas de ensamblaje.
Este enfoque permite fabricar motores de entre 0,75 a 18,7 kW (entre 1 y 25 CV), ideales para sistemas de climatización, maquinaria industrial ligera, pero también vehículos eléctricos de pequeño tamaño. La posibilidad de integrar el motor directamente en la rueda, sin ejes, diferenciales ni transmisiones intermedias, simplifica enormemente el sistema motriz, reduciendo pérdidas mecánicas y mejorando la eficiencia global.
Limitaciones del hierro como material magnético
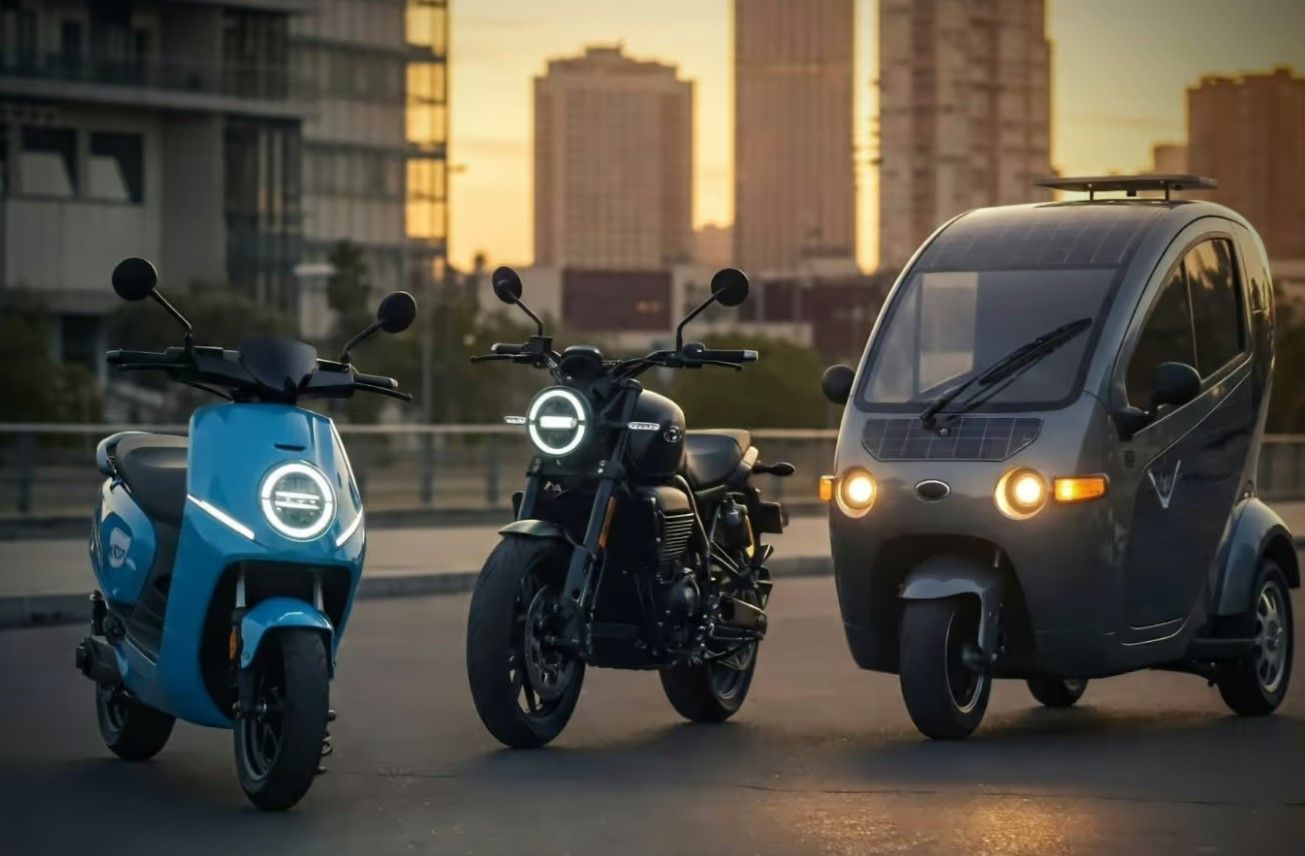
La desventaja intrínseca del hierro frente a los imanes de tierras raras es su menor densidad de flujo magnético, lo que conlleva una reducción de potencia específica. Por este motivo, este tipo de motores no es viable en vehículos eléctricos convencionales que requieren altos niveles de par y eficiencia a grandes velocidades, como turismos o SUV eléctricos.
Sin embargo, el diseño axial utilizado incorpora una disposición de masas magnéticas más alejada del eje de rotación, lo que, combinado con una mayor velocidad angular, permite aprovechar el efecto volante de inercia para mejorar el rendimiento en aplicaciones con ciclos de trabajo constantes, como ventiladores o compresores. Este comportamiento puede resultar ventajoso en escenarios donde la suavidad operativa y el mantenimiento simplificado priman sobre la respuesta dinámica pura.
Otro aspecto a considerar es el incremento de masa no suspendida en configuraciones en rueda, que puede comprometer la dinámica de conducción en vehículos ligeros. Aun así, el equilibrio entre simplicidad mecánica, independencia de cadenas logísticas críticas y reducción de costes de producción sitúa esta tecnología como una solución estratégica viable para electrificación ligera y descentralizada.
Ventajas clave del enfoque de Conifer
- Fabrica motores de 0,75–18,7 kW para usos como ventiladores HVAC, bombas o micro‑VE (scooters, ATVs, reparto urbano), sin dependencia de numismas de tierras raras.
- Su diseño permite producción en serie en la misma línea sin reequipamiento, reduciendo costes y tiempo.
- Utiliza bobinado plano automatizado, similar al de las baterías, que reduce costes en un 90% y acelera fabricación.
- Cada rueda puede llevar un motor independiente, evitando componentes tradicionales como ejes o diferenciales, y mejorando el control de tracción.
Fuente | Conifer