Volkswagen Group Components ha abierto la primera planta del Grupo para el reciclaje de baterías de coches eléctricos en Salzgitter. Con la planta piloto, el Grupo Volkswagen da otro paso comprometido hacia su objetivo de responsabilidad sostenible de extremo a extremo para toda la cadena de valor de la batería del vehículo eléctrico.
El objetivo es la recuperación industrializada de materias primas valiosas como litio, níquel, manganeso y cobalto en un bucle cerrado junto con aluminio, cobre y plásticos, logrando una tasa de reciclaje de más del 90% a largo plazo.
La característica única de la planta de Salzgitter es que solo recicla baterías que ya no se pueden utilizar para otros fines. Antes de reciclar la batería, un análisis determina si la batería sigue siendo lo suficientemente potente como para recibir una segunda vida en sistemas móviles de almacenamiento de energía, como la estación de carga rápida flexible o el robot de carga móvil.
Fase inicial
En la fase inicial el fabricante no espera grandes volúmenes de baterías hasta finales de la década de 2020 como muy pronto. Por lo tanto, la planta ha sido diseñada para reciclar inicialmente hasta 3.600 sistemas de baterías al año durante la fase piloto, lo que equivale a más de 1.600 toneladas. En el futuro, el sistema se puede escalar para manejar grandes cantidades, ya que el proceso se optimiza constantemente.
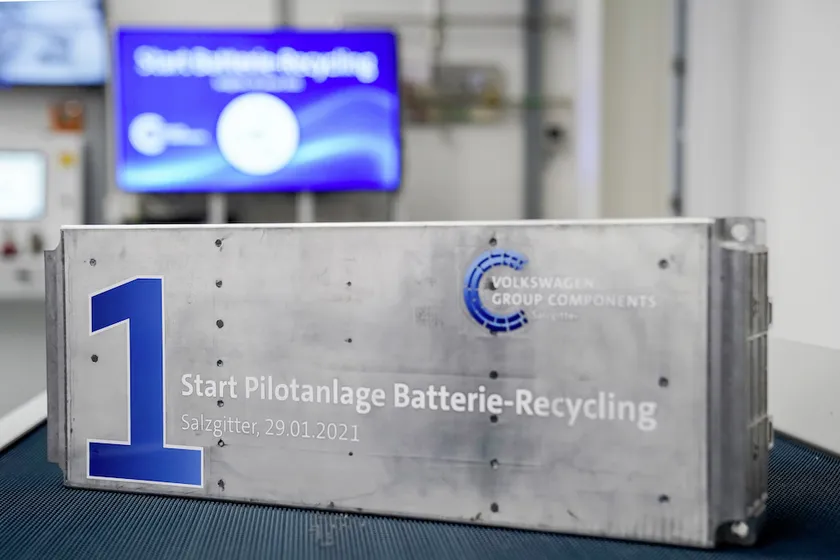
Thomas Schmall, miembro del Consejo de Administración de Volkswagen AG, División Técnica y Presidente del Consejo de Administración de Volkswagen Group Components, afirma que «Volkswagen Group Components ha logrado un paso más en su responsabilidad sostenible de extremo a extremo para la batería como un componente clave de la movilidad eléctrica».
Además Schmall indica que la compañía «está implementando un ciclo sostenible de materiales reciclables, y desempeña un papel pionero en la industria para un tema orientado al futuro con un gran potencial para la protección del clima y el suministro de materias primas«.
El proceso
El innovador proceso de reciclaje no requiere una fusión de uso intensivo de energía en un alto horno. Los sistemas de baterías usados se entregan, descargan profundamente y desmontan. Las partes individuales se muelen en gránulos en una trituradora y luego se secan.
Además del aluminio, el cobre y los plásticos, el proceso también produce un valioso «polvo negro«, que contiene las materias primas importantes para baterías como litio, níquel, manganeso y cobalto, así como grafito. La separación y procesamiento de las sustancias individuales por procesos hidrometalúrgicos, utilizando agua y agentes químicos, es llevado a cabo posteriormente por socios especializados.
«Como consecuencia, los componentes esenciales de las pilas de batería viejas se pueden utilizar para producir nuevo material de cátodo», explica Mark Möller, Jefe de la Unidad de Negocio de Desarrollo Técnico y Movilidad Electrónica.
Para Möller, a través «de la investigación, sabemos que las materias primas recicladas de la batería son tan eficientes como las nuevas. En el futuro, tenemos la intención de apoyar nuestra producción de pilas de batería con el material que recuperamos. Dado que la demanda de baterías y las materias primas correspondientes aumentará drásticamente, podemos hacer un buen uso de cada gramo de material reciclado«.
Fuente | VW, Rec Anything, YouTube