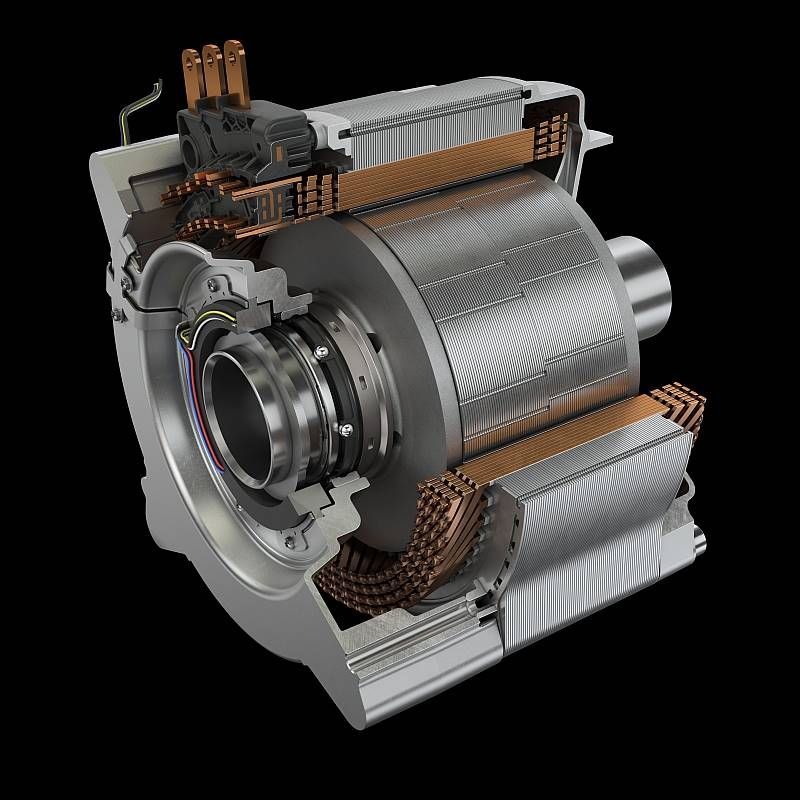
Mercedes abre su fábrica para reciclar baterías con un innovador proceso y reutilizarlas en sus coches eléctricos
Mercedes acaba de inaugurar en Kuppenheim, al sur de Alemania, una innovadora planta de reciclaje de baterías para coches eléctricos que logra el hito de usar, por primera vez en Europa, un proceso mecánico-hidrometalúrgico integrado.
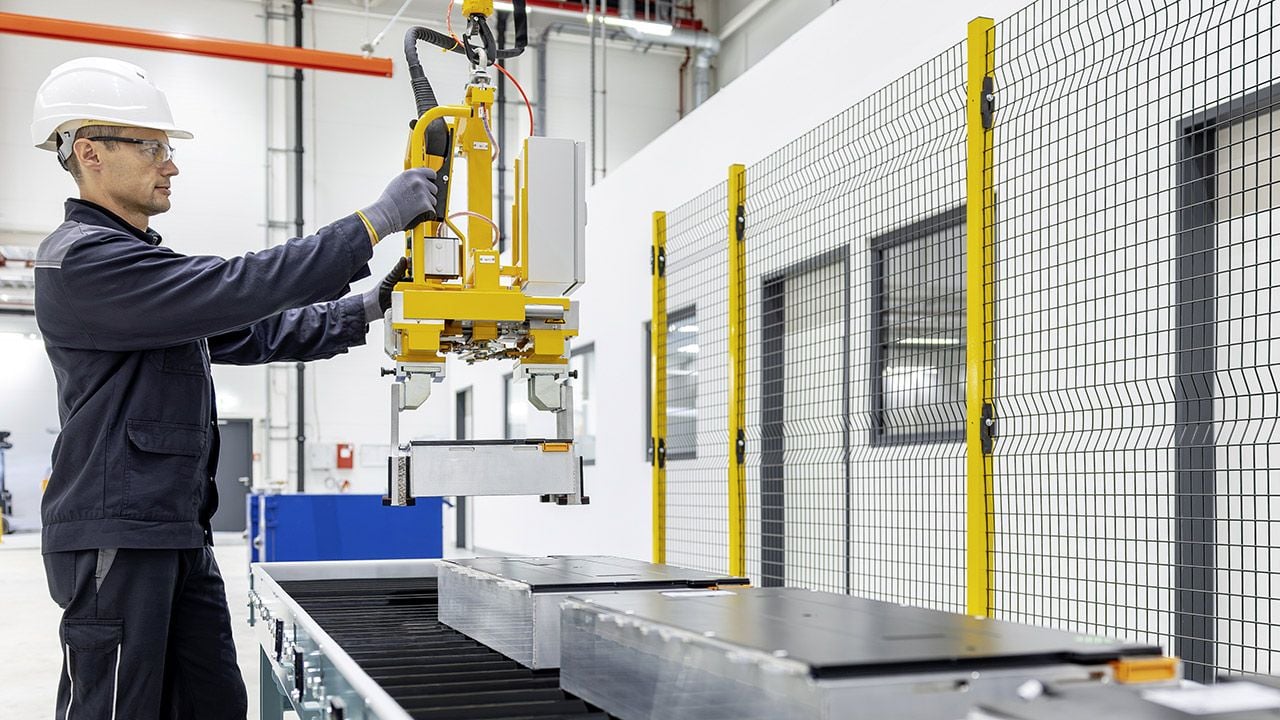
Al igual que el desarrollo de nuevos coches eléctricos, de nuevas fábricas para su producción, de producir más baterías y reducir la dependencia de los fabricantes y las empresas chinas, Europa tiene también una tarea pendiente con el reciclaje de dichas baterías. Mercedes es de las pocas marcas automovilísticas que cubren ya todo ese ciclo, gracias a la apertura de su propia fábrica para el reciclaje de baterías.
En Kuppenheim, en el sur de Alemania, la firma de la estrella acaba de estrenar la que es, además, la primera planta de reciclaje de baterías de Europa que utiliza un proceso mecánico-hidrometalúrgico integrado. Además, Mercedes asegura que es el primer fabricante de coches del mundo en cerrar el ciclo de reciclaje de baterías con sus propias instalaciones.
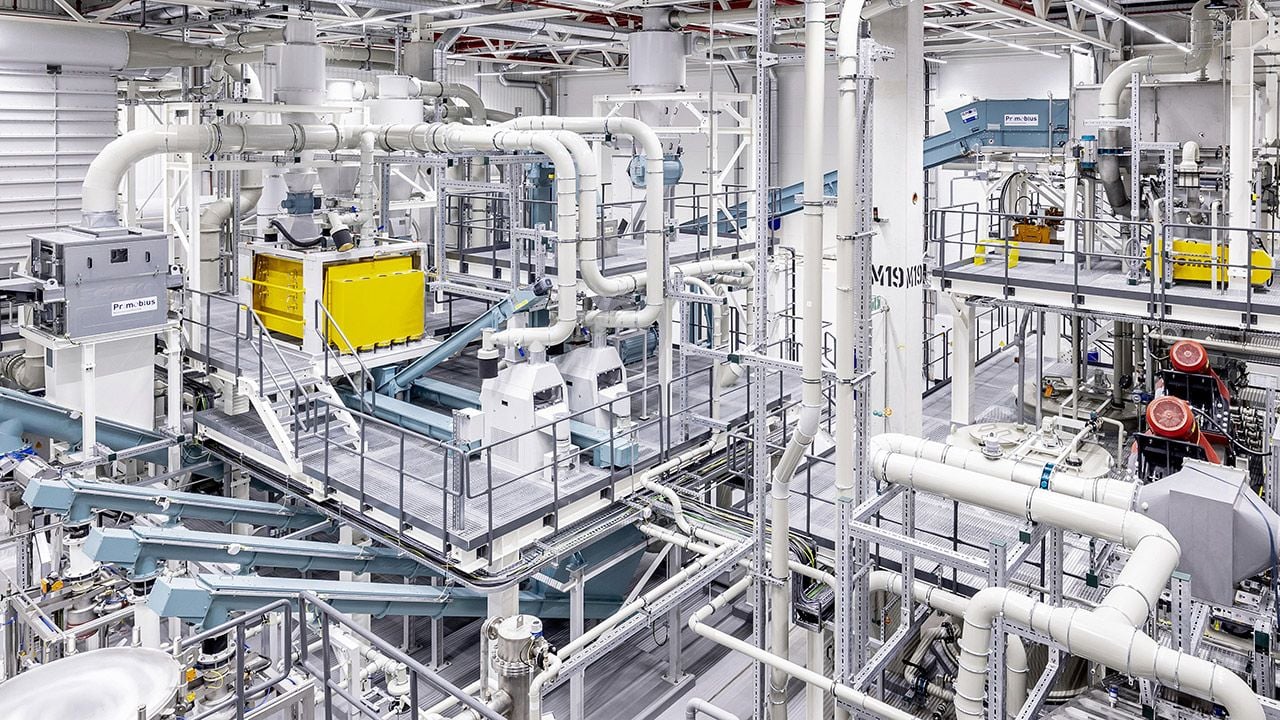
El proceso de economía circular con las baterías se cierra para la marca alemana con esa fábrica en la que han invertido decenas de millones de euros y que cuenta con la financiación del Ministerio Federal de Economía y Acción por el Clima de Alemania. Gracias a estas nuevas instalaciones, Mercedes asegura que podrá acceder a una tasa de recuperación de más del 96% y que podrá generar los suficientes materiales reciclados para producir más de 50.000 nuevos módulos de baterías cada año. En total, se espera tener una capacidad anual de 2.500 toneladas.
Y todo ello, en una nueva fábrica que opera de forma neutra en cuanto a emisiones de CO2 y con energía verde, gracias a una enorme instalación fotovoltaica en su techo. El innovador proceso mecánico-hidrometalúrgico se separa de la pirometalurgia que se ve hoy día en Europa y se beneficia de un proceso menos intensivo y que consume menos energía. El proceso mecánico se encarga de clasificar y separar plásticos, aluminio, hierro y cobre en diferentes fases; por su parte, el proceso hidrometalúrgico posterior se dedica ya a la masa negra, los materiales activos que forman los electrodos de las celdas de la batería.
Gracias a este proceso de reciclaje de Mercedes, que cubre todos los pasos desde la trituración de los módulos hasta el secado y procesado, pasando por la logística y la reintegración, la marca germana será capaz de recuperar materias primas valiosas y escasas como el cobalto, el níquel o el propio litio, pudiendo formar parte de nuevo en el futuro en los próximos coches eléctricos de Mercedes.
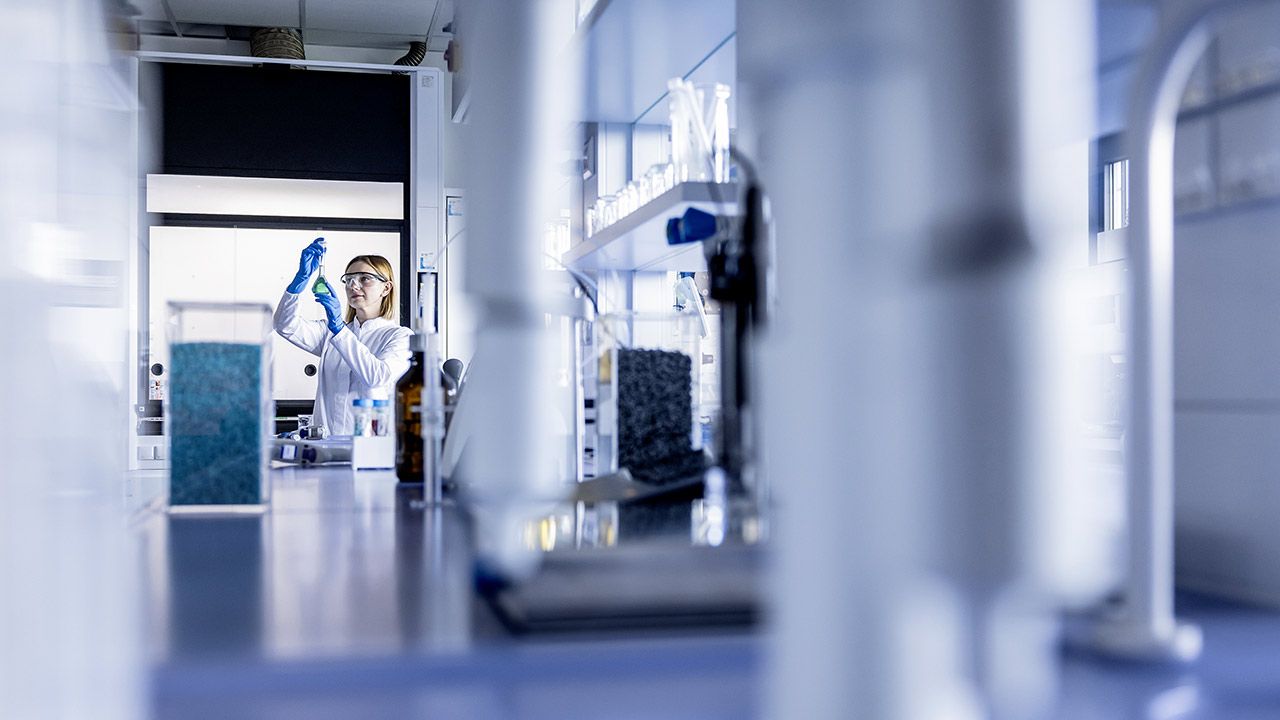
El fabricante alemán, que ofrece baterías reacondicionadas como piezas de repuesto para todos sus coches eléctricos, está asociada en este proyecto con Primobius, una importante empresa dedicada a la ingeniería mecánica y a los procesos, fruto de una empresa conjunta entre varios grupos. A este proyecto se le suma la inauguración del Mercedes-Benz eCampus, que trabajará en el desarrollo de nuevas químicas de celdas de baterías en Stuttgart-Untertürkheim.
«Estamos profundizando sistemáticamente nuestra experiencia en la cadena de valor de las baterías. La tecnología innovadora nos permite recuperar materias primas valiosas de la batería con el mayor grado de pureza posible. Esto convierte las baterías de hoy en la mina sostenible de materias primas del mañana», asegura Jörg Burzer, responsable de Producción, Calidad y Gestión de la Cadena de Suministro.